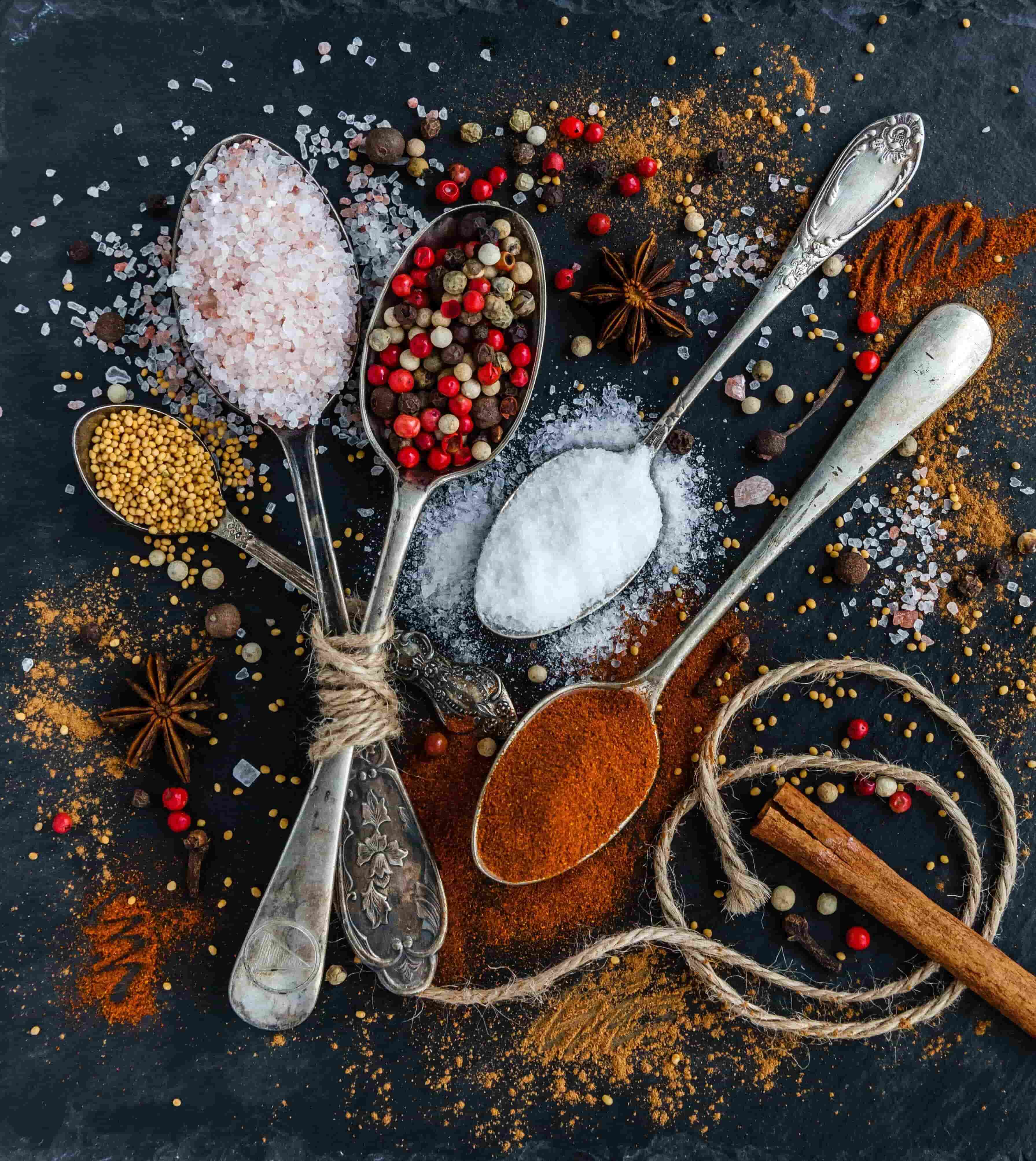
Blog
Product Yield - Flavor Manufacturing | Pall Corporation
March 3, 2021
As consumers across the globe continue their quest for global taste experiences, production of differentiated, flavor-infused products are on the increase. Demand for new and exciting flavors is often driven by a younger generation with a love for trying new things, and with a wealth of choice, flavor manufacturers are continuing to distinguish themselves by developing innovative products to meet demand. But with expanding flavor portfolios, flavor houses must also consider process efficiencies that save time and prevent product loss.
Traditional Filtration Methods: Are They Fit for Purpose?
Achieving the perfect flavor requires exceptional filtration to ensure a clear final product while removing particles that might spoil the final taste and flavor. To accomplish this, filtration products with filter-aids are often used in plate and frame systems.
Most common is the use of sparkler filters utilizing Diatomaceous Earth (DE) as a filter aid. Consisting of ancient skeletal remains of microscopic plants, DE offers an excellent filtration medium through its high pore volume and low resistance to flow. Unfortunately, there are also drawbacks to leveraging these methods. From insufficient final product quality requiring the reprocessing of the oils through to plugging of filters and the time taken to replace filters, this process can be time-consuming and labor-intensive.
This leads manufacturers to explore options that help them improve their operations, which in turn provides them numerous additional benefits.
How to improve process time and product yield in flavor manufacturing
One way to improve your process time is to look for filtration solutions that have high-flow capacity and therefore higher throughput thus reducing processing time. A solution that has high-flow increases throughput, thus reducing process time.
For example, Pall SUPRApak™ technology offers a unique high-area pack design called ‘edge-flow’, which provides great contact time of fluids with filter media.
Overcoming the disadvantages of conventional sparkler filtration methods, SUPRApak modules have a new flow configuration called “edge flow” which results in longer contact time of fluids with the filter media. The edge flow technology has excellent surface filtration and adsorption capability, which has been reported to significantly reduce process time by an average of 87% on average, resulting in a 700% productivity increase.
The ability to achieve extremely quick, one step single pass filtration eliminates the need for most filter aids and sparkler filters. Furthermore, filter changes of the SUPRApak module take around three minutes, which is around three times faster than other methods.
SUPRA modules not only help production processes, they also improve product yield. The SUPRApak system is a fully enclosed installation with low product hold-up volume. At the end of filtration, the housing can be pressurized with gas to empty the remaining fluid and therefore limit product losses. Because the ingredients used in flavors are so expensive, every last drop saved by leveraging SUPRA technology helps manufacturers reduce product loss, and in turn, cost.
Benefits Beyond Process Improvements and Product Yield
While manufacturers have seen both process time reduction and higher product yields by leveraging SUPRApak modules also address some other main challenges faced by flavor producers. Other SUPRApak technology benefits include:
- Reduced labor and process downtime due to low frequency and ease of SUPRApak module change-out and cleaning
- Sustainability improvements by reducing waste and in most cases, elimination of filter aids
- Improved product, personnel and environmental protection due to the enclosed system
Some of Pall's customers have reported increases of product quality up to 30% versus previous filtration methods.
As unique flavors continue to dominate the market, flavor houses need to adapt to meet consumer demand at a moment’s notice. With the right filtration solutions, manufacturers can not only meet demand by accelerating the total volumes produced, but also do so in an efficient manner.
To learn more about our solutions for flavors, please contact us.