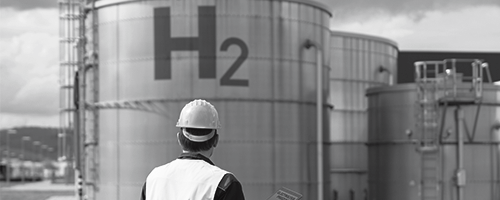
The Importance of Electrolyte Filtration in Green Hydrogen Production
Electrolyzers are the heart of green hydrogen production. These devices split water into hydrogen and oxygen when supplied with electricity. There are four types of electrolyzer technologies currently available – alkaline, PEM (polymer electrolyte membrane), SOEC (solid oxide electrolyzer cell) and AEM (anion exchange membrane).
The alkaline electrolyzer technology is the most mature and requires the lowest CAPEX. PEM electrolyzers are commercial but comparatively expensive while SOEC and AEM are still under demonstration. Consequently, alkaline electrolysis is the chosen technology for most of the largest green hydrogen projects announced globally.
The technology is called ‘alkaline’ because it uses a highly corrosive 30-40% potassium hydroxide (KOH) solution as the electrolyte feedstock. The electrolyte is under constant circulation within the electrolyzer (see figure 1) and will, over time, corrode the electrolyzer components, causing it to become contaminated with very fine particles.
Figure 1: Typical hydrogen electrolyzer configuration
Need for filtration
1) These fine particle contaminants, if not removed, can cause significant issues in green hydrogen production:The fine particles can accumulate and block small bore piping and bends within the electrolyzer, resulting in potentially catastrophic process upsets. In 1975, an explosion occurred at an electrolyzer facility in the UK. The incident investigation identified “blockage by sludge of the narrow electrolyte passages” as the main cause.
2) The fine particles contaminate other system components, such as electrodes and diaphragms, reducing their performance and service lifetime. The industry body IRENA highlights to “Mitigate catalyst poisoning/deactivation by foreign elements from electrolyte” as one of the key activities to improve the performance of alkaline electrolyzers. Electrode manufacturers have also started to insist on high-quality electrolyte cleanliness to ensure desired performance and lifetime of electrolyzers.
Electrolyte samples from an operating unit with a nominal filter (before) and after filtration through Pall's absolute rated filter. In the foreground, a sample of typical particulate contaminant removed from the electrolyte
How Pall can help
Each green hydrogen project is unique in its electrolyte filtration requirements. The alkaline electrolyzer technology being deployed varies considerably from one technology supplier to the next. Pall has a range of filtration solutions to suit every need. For Chemical Compatibility with Electrolyte, Pall can offer filter elements in polypropylene, polyphenylene sulfide, fluoropolymer or even high-alloy steel construction. For the removal of fine particles, Pall offers absolute-rated filters with sub-micron through 50-micron ratings.
However, before making a filter selection, the best practice is to understand the nature of contamination in the system. This helps select the correct filter that protects the customer’s electrolyzer at an optimal capex and opex. Pall’s experts can take samples from the customer’s operating unit and run a detailed contamination analysis determine the particle size distribution and chemical composition of particulates in the electrolyte. With this information, we can recommend the correct filter that is not too coarse (and allows contaminants to pass through) nor is too fine (necessitating shutdowns for frequent filter replacement).
- Category
- Author
- Sort By