Para proteger compresores, boquillas del quemador, unidades de aminas y glicol, tamices moleculares y lechos de protección de mercurio
Remover líquidos y sólidos de un flujo de gas es muy importante en las aplicaciones de refinería y procesamiento de gas. La remoción efectiva de estos contaminantes puede prevenir problemas costosos y tiempo de inactividad en los equipos del sector aguas abajo (downstream) como compresores, turbinas y quemadores. Asimismo, los hidrocarburos y contaminantes sólidos pueden formar espuma en una torre contactora con aminas y pueden contribuir al reemplazo prematuro del catalizador en los procesos catalíticos. En los compresores que usan aceite para lubricar cilindros, por lo general, el aceite lubricante ingresa al gas de descarga y provoca la contaminación en el sector aguas abajo. La fina película de hidrocarburos depositada en los intercambiadores de calor se espesará y formará coques, lo que disminuye la eficiencia de transferencia de calor, aumenta el consumo de energía y crea riesgo de puntos críticos y fugas.
Existen varias tecnologías que están disponibles para separar líquidos y sólidos de los gases. Este artículo primero brindará criterios de selección para las siguientes tecnologías de separación de gas/líquido:
- separadores por gravedad
- separadores centrífugos
- separadores de paletas con filtro
- almohadillas eliminadoras de niebla
- coalescedores de líquido/gas
y luego enfocarse en la separación de aerosoles finos de los gases usando tecnología de coalescencia líquido/gas.
Mecanismos de remoción
Antes de evaluar tecnologías específicas, es importante comprender los mecanismos que se usan para la separación de gases sólidos y líquidos. Estos se dividen en cuatro categorías diferentes². La primera y más fácil de comprender es la sedimentación por gravedad, que ocurre cuando el peso de las microgotas o partículas (es decir, la fuerza de gravedad) supera la resistencia que crea el flujo de gas.
Un mecanismo que está relacionado y es más eficiente es la separación centrífuga, que ocurre cuando la fuerza de gravedad supera la resistencia que crea el flujo de gas. La fuerza centrífuga puede ser muy superior a la fuerza de gravedad.
El tercer mecanismo de separación de gases sólidos y líquidos se denomina impacto inercial y ocurre cuando un gas pasa a través de una red, como fibras y barreras de choque. En este caso, el flujo de gas sigue un camino tortuoso a través de estos obstáculos mientras que las microgotas sólidas o líquidas tienden a seguir caminos más rectos e impactan en estos obstáculos. Una vez que sucede esto, la microgota o partícula pierde velocidad y se fusiona, y, al final cae al fondo del recipiente o queda atrapada en el medio de fibra.
Y, por último, un cuarto proceso de separación de gases líquidos y sólidos ocurre con aerosoles muy pequeños (menores que 0,1 µm). Este mecanismo se denomina intercepción difusional o movimiento browniano y ocurre cuando los pequeños aerosoles chocan con las moléculas de gas. Estos choques hacen que los aerosoles se desvíen del paso del flujo del líquido a través de las barreras, lo que aumenta la probabilidad de que golpeen contra una superficie de fibra y se eliminen³.
En esta página, las referencias al tamaño de las microgotas y las partículas serán en la unidad micrón. Un micrón es 1/1000 de un milímetro o 39/1.000.000 de una pulgada. La figura 1 muestra el tamaño de varios metales en micrones.
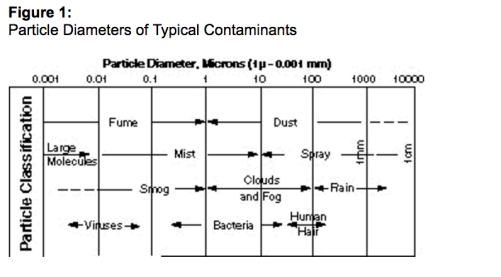
Mecanismos de remoción
Antes de evaluar técnicas específicas de separación de gases y líquidos, es importante comprender los mecanismos que se usan para eliminar los líquidos y sólidos de los gases. Se pueden dividir en cuatro categorías diferentes.2 La primera y más fácil de comprender es la sedimentación por gravedad, que ocurre cuando el peso de las microgotas o partículas (es decir, la fuerza de gravedad) supera la resistencia que crea el flujo de gas.
Un mecanismo que está relacionado y es más eficiente es la separación centrífuga, que ocurre cuando la fuerza de gravedad supera la resistencia que crea el flujo de gas. La fuerza centrífuga puede ser muy superior a la fuerza de gravedad.
El tercer mecanismo de separación de gases sólidos y líquidos se denomina impacto inercial y ocurre cuando un gas pasa a través de una red, como fibras y barreras de choque. En este caso, el flujo de gas sigue un camino tortuoso a través de estos obstáculos mientras que las microgotas sólidas o líquidas tienden a seguir caminos más rectos e impactan en estos obstáculos. Una vez que sucede esto, la microgota o partícula pierde velocidad y se fusiona, y, al final cae al fondo del recipiente o queda atrapada en el medio de fibra.
Y, por último, un cuarto mecanismo de separación de gases líquidos y sólidos ocurre con aerosoles muy pequeños (menores que 0,1 µm). Este mecanismo se denomina intercepción difusional o movimiento browniano y ocurre cuando los pequeños aerosoles chocan con las moléculas de gas. Estos choques hacen que los aerosoles se desvíen del paso del flujo del líquido a través de las barreras, lo que aumenta la probabilidad de que golpeen contra una superficie de fibra y se eliminen.3
En este artículo, las referencias al tamaño de las microgotas y las partículas serán en la unidad micrón. Un micrón es 1/1000 de un milímetro o 39/1.000.000 de una pulgada.
La figura 1 muestra el tamaño de varios metales en micrones.

Tecnologías de separación de líquido/gas
Separadores de gravedad
En un separador por gravedad o tambor de separación, las fuerzas gravitatorias controlan la separación. Cuanto menor sea la velocidad del gas y mayor sea el tamaño del recipiente, más eficiente será la separación líquido/gas. Debido al gran tamaño del recipiente que se necesita para alcanzar la sedimentación, raramente se diseñan separadores por gravedad para remover microgotas más pequeñas que 300 micrones⁴. Por lo general, se usa un depósito separador para la separación a granel, o como depurador de primera etapa. Un depósito separador también es útil cuando los componentes internos del recipiente deben ser mínimos, como en un sistema de alivio o en un servicio de contaminación⁵. Los separadores por gravedad no se recomiendan como la fuente única de remoción si se necesita una alta eficiencia de separación.
Separadores centrífugos
En los separadores centrífugos o ciclónicos, las fuerzas centrífugas pueden actuar sobre un aerosol con una fuerza varias veces mayor que la gravedad. Por lo general, los separadores ciclónicos se usan para remover aerosoles con un diámetro mayor que 100 µm y un ciclón de tamaño adecuado puede tener una eficiencia de remoción razonable de aerosoles tan pequeños como 10 µm. La eficiencia de remoción de un ciclón es muy baja en partículas de vaho más pequeñas que 10 µm⁶. Tanto los ciclones como los tambores separadores se recomiendan para materiales céreos o de coquización.
Almohadillas eliminadoras de niebla
El mecanismo de separación de gas líquido y sólido de las almohadillas antivaho es el impacto inerte. Por lo general, las almohadillas antivaho, que consisten en fibras o mallas tejidas pueden remover microgotas de hasta 1 a 5 micrones pero el recipiente que las contiene es relativamente grande porque deben operarse a velocidad baja para evitar el rearrastre de líquido.
Separador de paletas con filtro
Los separadores de paletas son simplemente una serie de deflectores o placas dentro de un recipiente. El mecanismo que controla la separación es, nuevamente, el impacto inercial. Los separadores de paletas son sensibles a la velocidad másica para la eficiencia de remoción, pero por lo general pueden operar a velocidades más altas que los antivaho, principalmente porque un drenaje más efectivo de líquidos reduce el rearrastre del líquido. Sin embargo, debido a las vías relativamente extensas entre las placas que constituyen la complicada red, los separadores de paletas solo pueden remover microgotas de tamaños relativamente grandes (10 micrones y más). A menudo, los separadores de paletas se utilizan para adaptar los recipientes de almohadillas eliminadoras de neblina cuando la velocidad del gas supera la velocidad de diseño⁷.
Filtros coalescentes de líquido/gas
Los cartuchos coalescentes de líquido/gas combinan las características de las almohadillas eliminadoras de neblina y los separadores de paletas, pero por lo general no se especifican para eliminar líquidos a granel. En los sistemas de líquido a granel, por lo general se coloca un coalescedor de alta eficiencia en el sector downstream de un tambor separador o de un separador de choque. El gas fluye a través de un paquete muy fino de material fibroso con una envoltura en la superficie exterior que promueve el drenaje del líquido (ver figura 2 a continuación). Un cartucho coalescente puede retener microgotas tan pequeñas como de 0,1 micrón. Cuando tienen el diseño y el tamaño adecuados, el drenaje de las microgotas coalescidas del paquete fibroso permite velocidades de gas mucho más altas que en el caso de las almohadillas antivaho y los separadores de paletas, sin rearrastre de líquido o aumento de la caída de presión en todo el conjunto.
La tabla 1 presenta un resumen de cada tecnología y brinda orientación para una selección adecuada. Como puede observar, para sistemas que contienen aerosoles muy finos, debajo de 5 µm, se debe escoger un coalescedor. Remover aerosoles muy finos de los gases genera mayores beneficios económicos, de fiabilidad y mantenimiento en sistemas con compresores.
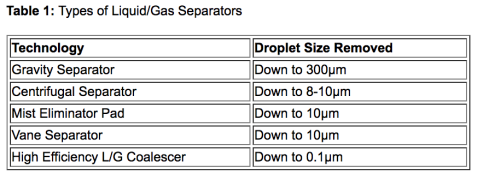
Formación de aerosoles finos
Hay varias formas diferentes en que los aerosoles líquidos muy finos pueden entrar en una corriente de gas.
• Condensación de un vapor saturado
• Atomización (efecto pulverizado a través de una restricción de flujo)
• Rearrastre de líquido8
Algunos estudios recientes sobre la distribución del tamaño de los aerosoles en un flujo de gas natural han identificado que una cantidad significativa de microgotas inferiores a 5 micrones es la norma donde hay válvulas de estrangulamiento u otras restricciones⁹ o cuando los vapores están en el punto de condensación¹⁰. Las medidas que se muestran en la figura 3 se tomaron para determinar la concentración de aerosoles líquidos en flujos de gas natural en el sector downstream de los separadores de paletas (combinación de separador por gravedad y barrera de filtro horizontal y equivalencia con almohadilla antivaho). Los resultados demuestran que, en muchos casos, la gran cantidad de aerosoles puede atravesar este tipo de separador porque las microgotas son muy pequeñas como para quedar atrapadas en estos dispositivos de separación. Como resultado, un coalescedor de líquido/gas debe ser la tecnología adecuada cuando se necesitan tasas altas de recuperación para proteger el equipo en el sector downstream o para recuperar productos líquidos valiosos.
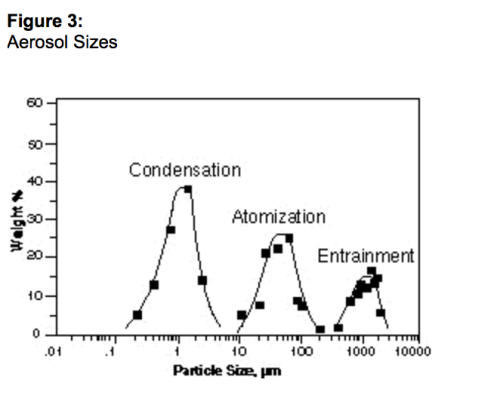
Clasificaciones y tamaños
Es importante destacar que un coalescedor es diferente de un filtro en el sentido de que realiza filtración de partículas sólidas finas y coalescencia de aerosoles líquidos de un flujo de gas. Los criterios de tamaño y clasificación de los coalescedores, en cuanto a la remoción de líquidos, son fundamentales para obtener el mejor rendimiento del coalescedor. Un coalescedor demasiado pequeño resultará en el rearrastre continuo de líquido, una muy baja eficiencia de separación de líquidos y gases, y será vulnerable a cualquier cambio del proceso. La naturaleza crítica del tamaño del coalescedor se ilustra en la figura 4, que muestra que el rendimiento del coalescedor puede disminuir muy rápidamente cuando el coalescedor se enfrente a demasiado líquido (ya sea por una concentración alta de aerosoles en el flujo de gas o por un caudal alto de gas). Esto marca una drástica diferencia con la mayoría de los equipos de separación cuyo rendimiento disminuye gradualmente a medida que se le exige más que su clasificación máxima.
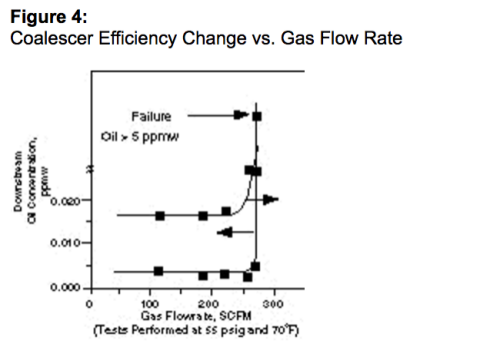
El método tradicional de validación del rendimiento de un coalescedor es la prueba de DOP (dioctil ftalato)¹¹. En esta prueba, la condensación de vapor de DOP bajo condiciones controladas genera continuamente un aerosol monodispersado de 0,3 µm de diámetro. Cuando se estabiliza la generación de aerosoles (tamaño de partículas constantes y concentración de aerosoles), se mide la concentración de DOP del coalescedor en el sector upstream y downstream con un fotómetro de dispersión de luz. Los resultados se expresan como un porcentaje de la penetración de DOP al caudal usado.
Algunas desventajas importantes de la prueba de DOP son las siguientes¹²
1. La prueba se realiza en un cartucho seco o insaturado. Un cartucho seco, en esencia, actúa como una esponja, absorbe cualquier líquido que pase. Lo que la prueba DOP no mide es la capacidad del coalescedor para retener líquidos cuando los líquidos saturan el medio del coalescedor y podrían volver a arrastrarse aguas abajo.
2. Esto genera una segunda desventaja. La caída de presión que se mide en el conjunto es subestimada cuando se compara con las caídas de presión reales en un elemento saturado. El DP saturado es aproximadamente 2-4 veces mayor que el DP limpio.
3. La prueba se realiza bajo un vacío parcial donde las propiedades del gas (densidad y viscosidad) son muy diferentes de las que prevalecen en la presión real de operación. Las condiciones de la prueba DOP tienden a exagerar la eficiencia del elemento coalescente.
Para evitar las deficiencias de la prueba de DOP, Pall ha desarrollado la prueba de LASE (eficiencia de separación de aerosoles líquidos). Esta prueba fue desarrollada exclusivamente para medir el rendimiento del coalescedor en un flujo de gas comprimido bajo condiciones más similares a las que se encuentran en una refinería o en una planta de procesamiento de gas. El sistema que se usa para esta prueba se representa en un esquema en la figura 5.
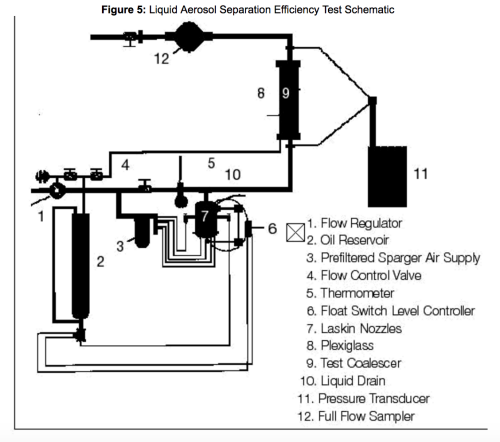
La prueba LASE se diferencia de la prueba de DOP de las siguientes formas:
1.Brinda una medición más precisa y significativa de la eficiencia. La eficiencia de DOP básicamente expresa el porcentaje de microgotas de dioctil ftalato de 0,3 µm que será removido por un coalescedor seco. La prueba de LASE expresa las ppmw de contaminantes que hay en el gas en el sector downstream del coalescedor. En otras palabras, lo que le dice la prueba LASE es a cuánto contaminante estará expuesto su equipo aguas abajo.
2. El DOP utiliza gotitas monodispersas (es decir, del mismo tamaño) de DOP, un líquido que no se encuentra comúnmente en el procesamiento de gas o en las corrientes de gas de refinería; la prueba LASE utiliza un aceite lubricante que tiene tamaños de gota que oscilan entre 0,1 y 0,9 µm.
3. La prueba LASE simula más de cerca las condiciones del proceso, ya que se ejecuta en un cartucho saturado y se realiza bajo presión positiva.
La tabla 2 muestra una comparación de la prueba de DOP y de LASE.
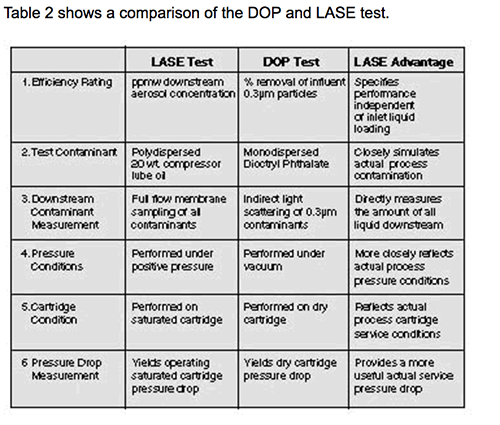
El diseño y su impacto en el tamaño
El objetivo de mejorar el diseño de los coalescedores es aumentar la eficiencia al mismo tiempo que evitamos el rearrastre de líquido. El rearrastre sucede cuando el gas de salida transporta microgotas de líquido acumuladas en un elemento coalescedor. Esto ocurre cuando la velocidad del gas que sale, o la velocidad anular, excede las fuerzas gravitatorias de la gota que drena.
Anteriormente hemos hablado de la importancia del tamaño correcto del coalescedor. Al diseñar y escoger un tamaño de coalescedor, se deben tener en cuenta los siguiente parámetros:
- Velocidad del gas a través del medio
- Velocidad anular del gas que sale por el medio
- Concentración de aerosoles líquidos y sólidos en el gas de entrada
- Capacidad de drenaje del coalescedor
Cada uno de estos factores pueden controlarse, excepto la concentración de aerosoles de entrada. Con un caudal de gas constante, la velocidad del medio se puede controlar ya sea cambiando la aspereza de la estructura de poros del medio o aumentando o disminuyendo la cantidad de cartuchos que se usan. Sin embargo, cuanto más grueso sea el medio, menos eficiente será el coalescedor para eliminar el líquido.
A un caudal de gas constante, la velocidad de salida del gas puede controlarse aumentando o disminuyendo el tamaño del recipiente o el espacio entre los cartuchos.
Se puede mejorar el drenaje ya sea seleccionando materiales del coalescedor con energía superficial baja o tratando el medio coalescedor con un químico que reduzca la energía superficial del medio a un valor más bajo que la tensión superficial del líquido que pasa por el coalescedor¹³. Contar con un material con energía superficial baja evita que el líquido humedezca el medio del filtro y acelere el drenaje por las fibras del medio. El líquido que pasa por el material fibroso del coalescedor cae rápidamente a través de la red de fibras sin acumularse en los poros donde se transportaría al gas y se rearrastraría. La figura 6 muestra el efecto que puede tener un tratamiento químico en el coalescedor. Muestra que el caudal máximo del cartucho con tratamiento químico es más del doble que en un cartucho similar sin tratamiento.

A partir de estos parámetros de diseño se puede concluir que una carcasa grande con una gran cantidad de cartuchos que tienen poros muy finos eliminaría los problemas de líquido que pueden encontrarse en el flujo del gas. Sin duda, los costos asociados con este recipiente son muy altos. A medida que se reduce la cantidad de cartuchos y el tamaño del recipiente, también se reduce la probabilidad de rearrastre y una eficiencia de remoción más baja. Además, a medida que disminuye el tamaño del conjunto del sistema, la caída de presión aumenta y puede aumentar los costos operativos. Entonces, se necesita una optimización. Al evaluar un diseño de coalescedor, asegúrese de que se tomen en cuenta todos estos parámetros para el tamaño del diseño. Se recomienda usar un coalescedor junto con un tambor separador u otro separador de choque.
Prueba de campo de coalescedores de líquido/gas
La prueba de campo de una corriente de gas donde es necesario eliminar los líquidos puede proporcionar la siguiente información:
1. la cantidad de liquido en el gas,
2. la capacidad de coalescer líquidos de manera eficiente, y
3. la cantidad de material particulado sólido presente.
Como resultado, un muestreo preciso es fundamental. Es muy importante medir con precisión los caudales de gas a través de un cartucho coalescente de prueba para determinar la cantidad y la naturaleza del líquido presente en el gas
Para ese objetivo, se ha diseñado un kit de prueba completa para realizar pruebas del coalescedor de líquido/gas del flujo lateral. Se muestra el kit de prueba en la figura 7. Incluye: (1) una carcasa del coalescedor para un cartucho conectado con una válvula esférica pequeña a un sumidero independiente; (2) un caudalímetro del orificio ade la carcasa del coalescedor en el sector downstream que incluye bridas, placa del orificio y calibrador de presión diferencial; (3) una válvula de aguja para regular el flujo de gas a través de la carcasa del coalescedor; (4) dos puertos de muestra, en los sectores upstream y downstream de la carcasa del coalescedor, a los que se pueden enganchar en simultáneo dos de los kits de prueba de gas con el fin de analizar la calidad del gas del afluente y el efluente; y (5) dos mangueras largas flexibles de acero inoxidable que conectan el kit de prueba con la línea de gas principal y la línea de descarga.

Procedimiento para las pruebas
Antes de ir al sitio para realizar una prueba de campo, se contacta a la planta para obtener información de las condiciones del sistema (presión, temperatura, caudal de gas, tipo de gas y, si es posible, concentración de líquido en el flujo de gas). En base a esta información, se selecciona una placa perforada para medir los caudales de gas en la gama indicada. El orificio también se selecciona para minimizar la caída de presión de modo que no se induzca la condensación de gas ni la formación de hidratos.
Después de colocar el kit de prueba del flujo lateral en línea, el caudal se ajusta por debajo del caudal crítico, para que no haya rearrastre. Una vez que el cartucho coalescente está saturado, se insertan las membranas de prueba en las plantillas de prueba de la carcasa del coalescedor en los sectores upstream y downstream, se vacía el sumidero de cualquier líquido que haya acumulado durante el período de saturación del cartucho, y comienza la prueba real.
Al final de la prueba, el volumen de líquido acumulado en el sumidero se mide y se recoge en una botella de muestra para su posterior análisis de laboratorio Las membranas de prueba también se juntan para determinar la cantidad de sólidos suspendidos en el gas para una identificación cualitativa de los contaminantes sólidos. La concentración de aerosoles líquidos está determinada por la cantidad de líquido coalescido y la cantidad de gas de muestra.
Resultados de la prueba de campo
Los resultados de las pruebas de campo de 49 flujos de gas (gas natural, dióxido de carbono, hidrógeno y gas combustible) tanto en plantas de procesamiento de gas y en refinerías demuestran que grandes cantidades de líquido están presentes en la mayoría de los flujos de gas. La figura 8 resume los resultados de las pruebas. De los 49 flujos probados, más del 85 % (43 de las 49 pruebas) tenía concentración de líquidos mayores que 1 ppmw. Esta concentración de líquido puede resultar en grandes problemas rotativos para el equipo y puede contribuir a operaciones deficientes de procesos en una unidad de contacto con aminas.

Conclusiones
1. Seleccionar las tecnologías de separación de gas/líquido no solo requiere conocer las condiciones del proceso, también las características de los contaminantes líquidos. La selección debe hacerse en función del tamaño de las gotas, la concentración y si el líquido tiene tendencias a la cera o al ensuciamiento.
2. A través de un análisis de datos de campo, se demostró que debido a la presencia de gotas de líquido muy finas (menos de 1 micrón) en la mayoría de los procesos de gas, se deben recomendar coalescedores de líquido/gas de alta eficiencia siempre que se requieran altas tasas de recuperación para proteger el equipo aguas abajo o para recuperar líquidos valiosos.
3. El tamaño y diseño del coalescedor es de gran importancia. Una vez que un coalescedor enfrenta demasiado líquido, ya sea debido a concentraciones excesivas de aerosol o a grandes caudales de gas, su eficiencia disminuirá rápidamente.
4. La prueba de eficiencia de separación de aerosol líquido (LASE) es una prueba de rendimiento significativa de los coalescedores de líquido/gas, ya que permite que los cartuchos coalescentes se prueben en condiciones que se asemejan mucho a las condiciones operativas reales (elemento saturado, caídas de presión realistas y propiedades del gas (densidad, viscosidad).
5. Un tratamiento superficial del medio coalescente mejoró el drenaje de líquidos en los materiales fibrosos y disminuyó en un 50 % la cantidad de cartuchos necesarios para manejar un flujo dado.
6. Las pruebas en el campo han demostrado que están presentes cantidades significativas de líquido en el flujo de gas de plantas de procesamiento de gas y en refinerías.
Referencias
1. CR Pauley, DG Langston y FC Betts, “Redesigned Filters Solve Foaming, Amine Loss Problems at Louisiana Gas Plant”, Oil & Gas Journal, 4 de febrero de 1991.
2. Manual de ingenieros químicos de Perry, sexta edición, McGraw-Hill, Nueva York, 1984, cap. 18, págs. 48-56.
3. Manual de ingenieros químicos de Perry, sexta edición, McGraw-Hill, Nueva York, 1984, cap. 18, págs. 48-56.
4. KJ Fewel Jr., JA Kean, “Modelado por computadora ayuda a la modificación del separador”, Oil & Gas Journal, 6 de julio de 1992.
5. AK Coker, “El programa informático mejora las pautas para los diseños de separación de gas y líquido”, Oil & Gas Journal, 10 de mayo de 1993.
6. Manual de ingenieros químicos de Perry, sexta edición, McGraw-Hill, Nueva York, 1984, cap. 18, págs. 48-56.
7. KJ Fewel Jr., JA Kean, “Modelado por computadora ayuda a la modificación del separador”, Oil & Gas Journal, 6 de julio de 1992.
8. Manual de ingenieros químicos de Perry, sexta edición, McGraw-Hill, Nueva York, 1984, cap. 18, págs. 48-56.
9. CAG Regan y M. Baker, “A Novel Separator/Scrubber Design Program - The Impact of Upstream and Downstream Equipment on Separation Performance”, artículo presentado en la 9ª Reunión Continental de la Asociación de Procesamiento de Gas, Capítulo Europeo, 14 y 15 de mayo de 1992 .
10. Manual de ingenieros químicos de Perry, sexta edición, McGraw-Hill, Nueva York, 1984, cap. 18, págs. 48-56.
11. C. Dickenson, “Filters and Filtration Handbook,” 3rd Edition, Elsevier Adv. Tech, Oxford, 1992, págs. 44-47.
12. K. Williamson, S. Tousi y R. Hashemi, "Recent Developments in Performance Rating of Gas/Liquid Coalescer", artículo presentado en la 1.ª reunión anual de la American Filtration Society, del 21 al 25 de marzo, Ocean City, MD.
13. J. D. Miller, E. E. Koslow, K. W. Williamson, U. S. Patent 4,676,807, 30 de junio, 1987; id., U. S. Patent 4,759,782, 26 de julio, 1988.
Nuestros productos
Lideramos la industria con soluciones de productos que se adaptan a las necesidades de nuestros clientes.