Beware the Electrostatic Storm in your fluid system
With demand for higher turbine speeds, increased operating pressures, and more demanding duty cycles, using highly refined, lower conductivity, finely filtered fluids, more and more Power Plant operators are experiencing the impact of electrostatic discharge (ESD) and the formation of ‘varnish’ in their turbine lubrication and hydraulic control systems
Varnish is an insoluble film deposit that forms on surfaces inside fluid systems, including pipes, tanks, bearings, heat-exchangers, and servo-valves. These deposits can cause operation problems, clogging valves and coating bearings to make them less effective and ultimately to fail.
Why is electrostatic discharge happening?
When two dissimilar materials are placed in contact and then separated in a sliding motion, it results in electron transfer between the two materials and the creation of static. This occurs when synthetic fluids passing through synthetic filter media, generating electrostatic charges, sometimes referred to as triboelectric charging.
The charge, if not dissipated, can build to the point where it causes high voltage sparks to jump to the closest metallic point, burning and degrading the oil, often blasting holes through filter media and damaging system components. And damaged parts cannot do their jobs.
Like a lightning bolt in your fluid system.
For a number of years, many ignored this phenomenon. But as problems have worsened, people are paying more attention.
Standard glass-fiber media installed in the lube system can potentially experience severe electrostatic-induced damage in a short time. Heat exchangers, flowmeters, valves, filter housing, and filter elements can all experience damage. Also, as fluids can break down, resulting in thermal degradation/varnish formation, premature additive depletion, and reduced fluid service life. Electrical arcing can also pose a safety hazard, causing injury, fires or even explosions.
How would I know it’s happening?
- Stand beside a filter where discharge is occurring, you will hear a harsh knocking, crackling or pinging sound from within
- You may notice burn marks on the filtration medium when changing out filters
- Most likely you will see the visible results of ESD with all wetted surfaces of pipes and components being coated in a resinous film coating
Modern turbine lube oils are highly refined API group II oils, meaning they are less polar and have low conductivity (5-40 pS/m range). Electrostatic discharges result in changes in the chemical composition of the fluids, changing nonpolar molecules to polar molecules, which act as precursors to the formation of varnishes.
Electrostatic Discharge & Varnish White Papers
-
Overcoming Electrostatic Charge Generation
Enter your details to download
Download: -
Electrostatic Charge Generation In Hydraulic Lubrication Systems
Enter your details to download
Download: -
Effective Varnish Removal from Turbine Lubrication Systems
Enter your details to download
Download:
What can I do to stop it?
While some equipment manufacturers are only just starting to understand the impacts electrostatic build-up and discharge, Pall has been designing filters capable of preventing the effects of ESD since early 2000’s.
Pall customers enjoy the protection provided by anti-static media using Pall Athalon® Filters that not only ensure against electrostatic discharge, but also has higher dirt capacity, lower pressure drop, longer service life, and larger surface area for fluid contact.
Other methods such as grounding filter housings and pipes as a preventative safety measure, can reduce external discharging, but cannot stop fluid charge generation or internal damage to the filter or other system components caused by sparking.
Anti-static additives are used but are not recommended for lube oils. Static charge reducers – an electrical devise, the use of conductive metal mesh in filter construction or lowering the velocity of the oil going through the filter or increasing the size of the filter are all options but not technically or economically viable, especially for existing lube oil systems. With Athalon anti-static filters you prevent the problem at the root cause.
What can I do if I already have varnish in my system?
The use of an adsorbent filter media to attract and retain the varnish forming material from the oil is an effective method using a filter media that has high affinity for the varnish material that is polar in nature.
The Pall Varnish Removal Filter or VRF works on the basis of physiosorption. It is not a chemical reaction so does not add or remove anything from the oil. As the oil is cleaned of varnish, it dissolves the varnish deposited on surfaces, thus slowly cleaning the oil and the surfaces over time.
Choose Pall for prevention and removal of turbine lube system varnish.
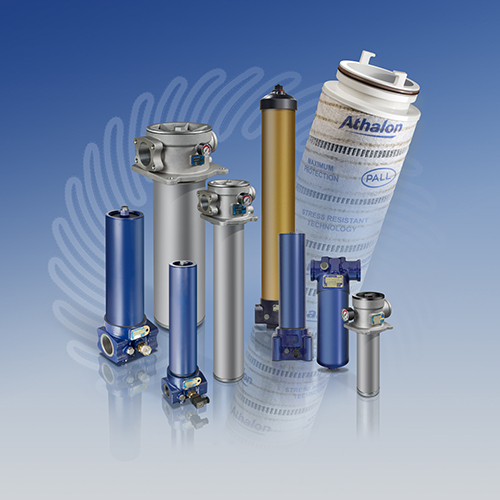
For prevention and removal of turbine lube system varnish.