Para proteção de compressores, bico de queimadores, unidades de amina e glicol, peneiras moleculares e leitos de proteção de mercúrio
Introdução
Remoção de líquido e sólidos da corrente de gás é muito importante no refino e processamento de gás . A remoção eficaz desses contaminantes pode evitar problemas custosos e tempo de inatividade dos equipamentos a jusante, como compressores, turbinas e queimadores. Além disso, hidrocarbonetos e contaminantes sólidos podem induzir a formação de espuma em uma torre de contato de amina e podem contribuir para trocas prematuras de catalisador em processos catalíticos. Em compressores que usam óleo para lubrificar cilindros, o óleo lubrificante geralmente entra no gás de descarga causando contaminação da corrente a jusante. Uma película fina de hidrocarboneto depositada nos trocadores de calor engrossará e sofrerá coqueamento, diminuindo a eficiência da transferência de calor, aumentando o consumo de energia e criando risco de pontos de calor e vazamentos.
Tipos de mecanismos de remoção para retirar líquidos e sólidos dos gases
Antes de avaliar tecnologias específicas de separação de gás e líquido, é importante entender os mecanismos usados para remover líquidos e sólidos de gases. Eles podem ser divididos em quatro categorias diferentes.2
Sedimentação por gravidade
A primeira e mais fácil de entender é a decantação por gravidade, que ocorre quando o peso das gotas ou partículas (ou seja, a força gravitacional) excede o arrasto criado pelo gás em fluxo.
Separação centrífuga
Um mecanismo mais eficiente é a separação centrífuga que ocorre quando a força centrífuga escede o arrasto criado pelo fluxo do gás. A força centrífuga pode ser várias vezes maior que a força gravitacional.
Impacto inercial
O terceiro mecanismo de separação de gás líquido/sólido é chamado de impacto inercial, que ocorre quando um gás passa através de uma rede como, por exemplo, barreiras de fibras e de choque. Neste caso, a corrente de gás segue um tortuoso caminho em torno dos obstáculos, enquanto as gotículas sólidas ou líquidas tendem a seguir caminhos mais lineares, impactando nos obstáculos. Uma vez que isso ocorre, a gotícula ou partícula perde velocidade e/ou coalesce e, eventualmente, cai para o fundo do tanque ou permanece presa ao material filtrante de fibra.
Separação de gás líquido/sólido
E, finalmente, um quarto mecanismo de separação de gás líquido/sólido ocorre com aerossóis muito pequenos (menos de 0,1 µm). Chamado de interceptação difusional ou movimento Browniano, esse movimente ocorre quando pequenos aerossóis colidem com móleculas de gás. Essas colisões fazem com que aerossóis se desviem do caminho do fluxo de fluido em torno das barreiras, aumentando a probabilidade de os aerossóis atingirem a superfície da fibra e serem removidos.3
Ao longo deste artigo, as referências aos tamanhos de gotas e partículas estarão na unidade micrômetro. Um mícron é 1/1000 de um milímetro ou 39/1.000.000 de uma polegada.
A figura 1 mostra o tamanho de diversos materiais em micrômetros.
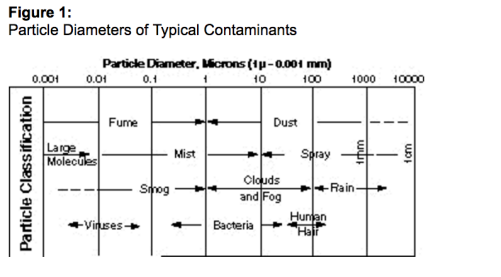
Tipos de separadores líquido/gás e tecnologias utilizadas neles
Diversas tecnologias estão disponíveis para separação de gás líquido e gás sólido . Este artigo irá fornecer os primeiros critérios de seleção para as seguintes tecnologias de separação líquiso/gás:
- separadores por gravidade
- separadores centrífugos
- separadores de filtro por palhetas
- placas eliminadoras de névoas
- coalescedores líquido/gás
e em seguida focar na separação de aerossóis finos em gases usando a tecnologia de coalescência de líquido/gás
Separadores por gravidade
Em um separador por gravidade ou tambor knock-out, as forças gravitacionais controlam a separação. Quanto menor a velocidade do gás e maior o tamanho do tanque, mais eficiente será a separação líquido/gás. Devido ao grande tamanho do tanque necessário para atingir o assentamento, os separadores por gravidade raramente são projetados para remover gotículas menores que 300 mícrons⁴. Um vaso knock-out geralmente é usado para separação em massa ou como raspador de primeiro estágio. Um vaso knock-out também é útil quando a parte interna do vaso deve ser mantida em um mínimo, como em um sistema de alívio ou em serviço de incrustação⁵. Separadores por gravidade não são recomendados como a única fonte de remoção se for necessária alta eficiência de separação.
Separadores centrífugos
Em separadores centrífugos ou ciclone, as forças centrífugas podem atuar em um aerossol com uma força várias vezes maior que a gravidade. Geralmente, separadores ciclônicos são utilizados para remover aerossóis maiores do que 100 µm de diâmetro e um ciclone de tamanho adequado pode ter uma eficiência de remoção razoável de aerossóis inferiores a 10 µm. A eficiência de remoção do ciclone é muito baixa em partículas de névoa menores do que 10 µm⁶. Tanto os ciclones quanto os vasos knock-out são recomendados para materiais cerosos ou formadores de coqueamento.
Eliminadoras de névoa
O mecanismo de separação de placas eliminadoras de névoas é o impacto inercial. Geralmente, as placas eliminadoras de névoas, consistindo de fibras ou malhas trançadas, podem remover gotículas de até 1 a 5 micrômetros, mas o tanque que as contêm é relativamente grande porque ele precisa ser operado em velocidades baixas para evitar a reentrada de líquido.
Separadores de palhetas do filtro
Os separadores de palhetas são simplesmente uma série de defletores ou placas dentro de um vaso. O mecanismo que controla a separação novamente é a impactação inercial. Os separadores de palhetas são sensíveis à velocidade de massa para eficiência de remoção, mas geralmente podem operar em velocidades mais altas do que os eliminadores de névoa, principalmente porque uma drenagem de líquido mais eficaz reduz a reentrada de líquido. No entanto, devido aos caminhos relativamente grandes entre as placas que constituem a rede tortuosa, o separador de palhetas só pode remover tamanhos de gotículas relativamente grandes (10 mícrons e maiores). Freqüentemente, os separadores de palhetas são usados para modernizar os vasos do eliminador de névoa quando a velocidade do gás excede a velocidade do projeto⁷.
Coalescedores líquido/gás
Os cartuchos coalescedores de líquido/gás combinam recursos dos eliminadores de névoa e os separadores de palhetas, mas geralmente não são especificados para remover líquidos a granel. Em sistemas de líquido a granel, um coalescedor de alta eficiência geralmente é instalado a jusante de um vaso knock-out ou do separador de impacto. O gás flui através de um pacote muito fino de material fibroso ligado com um envoltório na superfície externa para promover a drenagem do líquido (consulte a Figura 2, abaixo). Um filtro coalescente pode reter gotículas menores de até 0,1 micron. Quando corretamente projetado e dimensionado, a drenagem das gotículas coalescidas do pacote fibroso permite velocidades de gás muito mais altas do que no caso das placas eliminadores de névoas ou separadores de palhetes, sem reentrada de líquido ou aumento na queda de pressão na montagem.
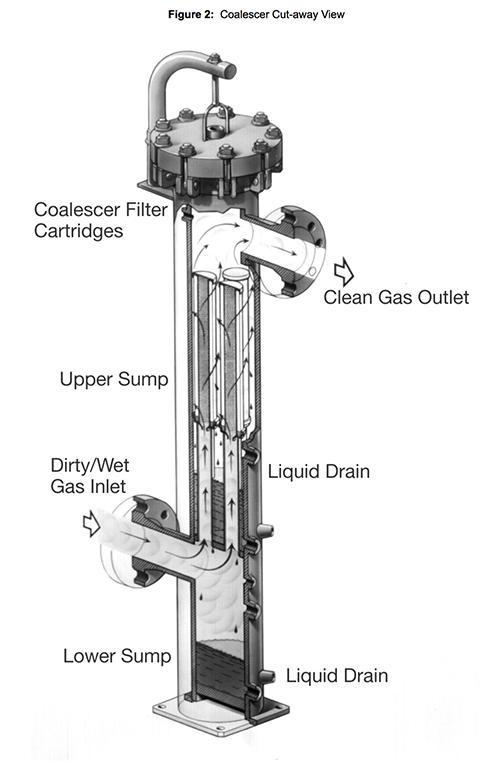
A tabela 1 resume cada uma dessas tecnologias e oferece orientações para a escolha correta. Como pode ver, para sistemas contendo aerossóis muito finos, abaixo de 5 µm, um coalescedor deve ser selecionado. Remover aerossóis muito finos dos gases resulta em grande economia, confiabilidade e benefícios de manutenção em sistemas de compressor.
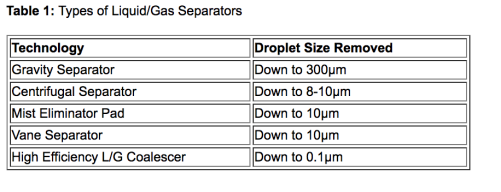
Formação de aerossóis finos
Há diversos modos pelos quais aerossóis líquidos muito finos podem entrar no fluxo de gás.
1. Condensação de um vapor saturado,
2. Atomização (efeito de pulverização através de uma restrição de fluxo) e,
3. Reentrada de líquido
Estudos recentes sobre a distribuição do tamanho dos aerossóis em fluxos de gás natural identificaram que quantidades significativas de gotículas abaixo de 5 mícrons são o padrão sempre que válvulas de estrangulamento e outras restrições estiverem presentes⁹ ou quando vapores estiverem em seus pontos de condensação¹⁰. As medidas mostradas na Figura 3 foram realizadas para determinar a concentração de aerossóis líquidos na corrente de gás natural amostrada a jusante de separadores de palhetas (combinação do separador por gravidade e barreira de filtro horizontal e equivalente a um eliminador de névoa Demist). Os resultados mostram que em muitos casos, grandes quantidades de aerossóis podem passar por esse tipo de separador porque as gotas são muito pequenas para serem retidas por esses dispositivos de separação. Como resultado, um coalescedor líquido/gás deve ser a tecnologia de escolha sempre que altas taxas de recuperação forem necessárias para proteger equipamentos a jusante ou para recuperar valiosos produtos líquidos .
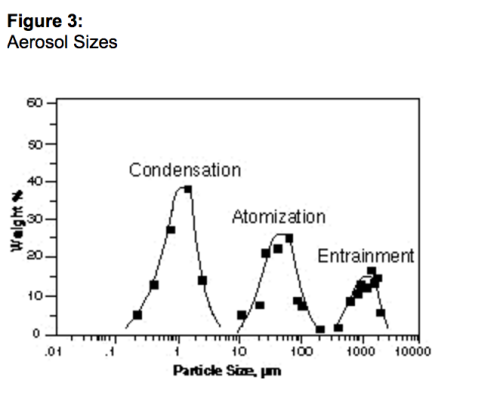
Classificações/dimensionamento
É importante notar que um coalescedor é diferente de um filtro, pois realiza tanto a filtração de partículas sólidas finas quanto a coalescência de aerossóis líquidos de uma corrente de gás. Os critérios de dimensionamento e classificação para coalescedores, no que se refere à remoção de líquidos, são muito críticos para o desempenho final do coalescedor. Um coalescedor subdimensionado resultará em reentrada contínua de líquido, eficiência muito baixa de separação de líquido do gás e será vulnerável a quaisquer alterações de processo. A natureza crítica do dimensionamento do coalescedor é ilustrada na Figura 4, onde mostra que o desempenho do coalescedor pode cair muito rapidamente quando o coalescedor é desafiado com muito líquido (seja por alta concentração de aerossol no fluxo de gás ou por causa de uma alta vazão de gás). Este é o maior registro da diferença entre a maioria dos outros equipamentos de separação cuja performance diminui gradualemnte à medida que é empurrado para além do seu máximo.
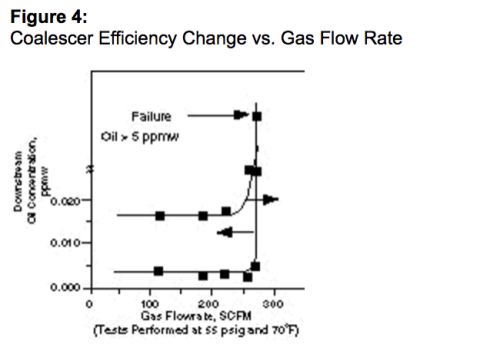
O meio tradicional de validação do desempenho do coalescedor é o teste DOP (dioctilftalato)¹¹. Neste teste, um aerossol monodisperso de 0,3 µm de diâmetro é gerado continuamente por uma condensação de vapor DOP sob condições controladas. Quando a geração de aerossol é estabilizada (tamanho de partícula constante e concentração de aerossol), a concentração de DOP é medida a montante e a jusante do coalescedor por um fotômetro de dispersão de luz. Os resultados são expressos como uma porcentagem de penetração de DOP na taxa de fluxo usada.
Algumas das principais desvantagens do teste DEHP incluem¹²
1. O teste é realizado em um cartucho seco ou insaturado. Um cartucho seco, em essência, age como uma esponja, absorvendo qualquer líquido que passe por ele. O que o teste DOP não mede é a capacidade do coalescedor de reter líquidos quando os líquidos saturam o meio do coalescedor e podem reintegrar a corrente a jusante.
2. Isso leva a uma segunda desvantagem; a queda de pressão medida no conjunto é subestimada quando comparada com as quedas de pressão reais em um elemento saturado. O DP saturado é aproximadamente 2-4 vezes maior que o DP limpo.
3. O teste é realizado sob vácuo parcial, onde as propriedades do gás (densidade e viscosidade) são muito diferentes daquelas prevalecentes na pressão real de operação. As condições de teste DOP tendem a superestimar a eficiência do elemento coalescedor.
Para evitar falhas no teste DOP, a Pall desenvolveu o teste de eficiência de separação de aerossol líquido (LASE). Este teste foi desenvolvido exclusivamente com a finalidade de medir o desempenho do coalescedor em uma corrente de gás comprimido em condições mais semelhantes às encontradas em uma refinaria ou planta de processamento de gás. O sistema utilizado para este teste está representado esquematicamente na Figura 5.
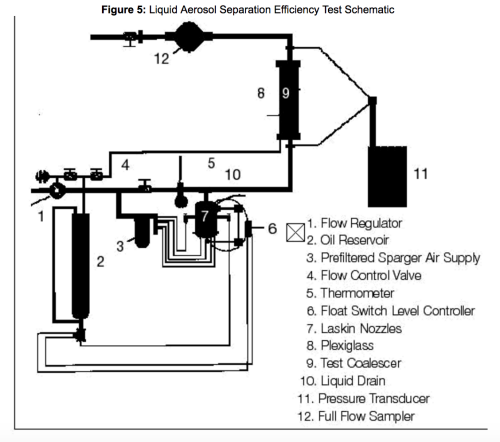
O teste LASE difere do teste DEHP das seguintes maneiras:
1. Ele fornece uma medida mais precisa e significativa da eficiência. A eficiência DOP essencialmente informa qual porcentagem de gotículas de dioctilftalato de 0,3 µm serão removidas por um coalescedor seco; o teste LASE informa quantos ppmw de contaminantes estarão no gás a jusante do coalescedor. Em outras palavras, o que o teste LASE lhe diz é a quantidade de contaminantes a que seu equipamento posterior estará exposto.
2. O DOP usa gotículas monodispersas (ou seja, do mesmo tamanho) de DOP, um líquido não comumente encontrado em um processamento de gás ou fluxos de gás de refinaria; o teste LASE usa um óleo lubrificante com tamanhos de gotículas que variam de 0,1 a 0,9 µm.
3. O teste LASE simula mais de perto as condições do processo, sendo executado em um cartucho saturado e realizado sob pressão positiva.
A tabela 2 mostra uma comparação do teste DOP e LASE.
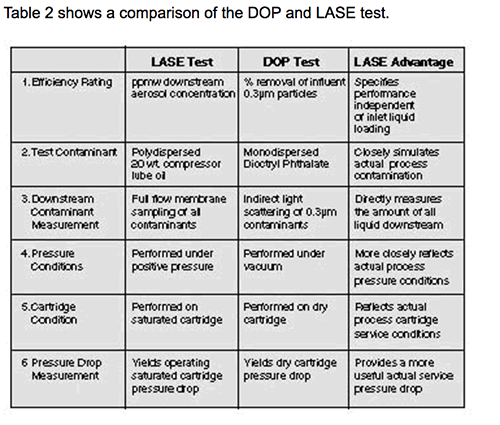
Design e seu impacto no dimensionamento
O objetivo de melhorar o design do coalescedor é maximizar a eficiência enquanto evita a reentrada de líquido. A reentrada ocorre quando gotículas de líquido acumuladas em um elemento do coalescedor são transportadas para fora pelo gás que sai. Isso ocorre quando a velocidade do gás de saída, ou a velocidade anular, excede as forças gravitacionais da gota drenada
Anteriormente discutimos a importância do dimensionamento correto do coalescedor. Ao projetar e dimensionar um coalescedor, os seguintes parâmetros precisam ser levados em consideração:
- Velocidade do gás pelo material filtrante,
- Velocidade anular do gás que sai da mídia,
- Concentração de sólidos e líquidos no gás de entrada, e
- Capacidade de drenagem do coalescedor
Cada um desses fatores, com exceção da concentração do aerossol de entrada, pode ser controlado. Em uma vazão de gás constante, a velocidade no meio pode ser controlada tanto pela troca da espessura da estrutura de poros do material filtrante, quanto pelo aumento ou redução do número de cartuchos utilizados. Quanto mais grosso o meio, no entanto, menos eficiente será o coalescedor na remoção do líquido.
Com uma taxa de fluxo de gás constante, a velocidade de saída do gás pode ser controlada aumentando ou diminuindo o tamanho do vaso ou o espaço entre os cartuchos
A drenagem pode ser melhorada selecionando-se materiais coalescentes com baixa energia superficial ou tratando o material filtrante do coalescedor com um produto químico que reduza a energia superficial do material filtrante até um valor inferior àquele da tensão da superfície do líquido a ser coalescido¹³. Ter um material com energia superficial baixa evita que o líquido umedeça o material filtrante e acelere a drenagem dos líquidos pelas fibras do material filtrante. O líquido coalescido no material fibroso cai rapidamente pela rede de fibras, sem acumular nos poros onde ele, de outro modo, seria empurrado pelo gás e reinserido. A Figura 6 mostra o efeito de um tratamento químico em um coalescedor. Ela mostra que a vazão máxima de um cartucho tratado quimicamente é mais de duas vezes aquela de um cartucho similar que não é tratado.
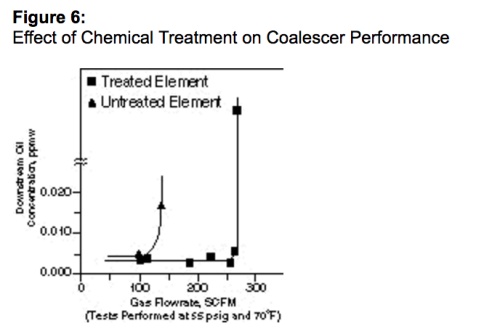
Pode-se concluir a partir desses parâmetros de projeto que uma grande carcaça com um grande número de cartuchos com poros muito finos eliminaria facilmente quaisquer problemas de líquido que você possa encontrar em um fluxo de gás. Obviamente, os custos associados a tal vaso são muito altos. À medida que o tamanho do vaso e a quantidade de cartuchos são reduzidos, há a probabilidade de reentrada e menor eficiência de remoção. Além disso, conforme o tamanho do conjunto diminui, a queda de pressão aumenta, o que pode resultar em custos operacionais maiores. Então, otimização é necessária. Ao avaliar o conjunto coalescente, certifique-se de que todos esses parâmetros sejam levados em consideração quando o conjunto for dimensionado. Um coalescedor é melhor utilizado em conjunto com um vaso knock-out ou outro separador de impacto.
Teste de campo para coalescedores líquido/gás
Um teste de campo de um fluxo de gás onde os líquidos precisam ser removidos pode fornecer as seguintes informações:
1. a quantidade de líquido no gás,
2. a capacidade de coalescer líquidos de forma eficiente, e
3. a quantidade de material particulado sólido presente.
Como resultado, amostras precisas se tornam essenciais. É muito importante medir com precisão as taxas de fluxo de gás através de um cartucho coalescedor durante o teste para determinar a quantidade e a natureza do líquido presente no gás.
Para esse fim, um kit de teste completo foi projetado para executar o teste do coalescedor líquido/gás em um fluxo lateral. Esse kit de teste é mostrado na Figura 7. Ele inclui: (1) um vaso coalescedor para um filtro conectado a um reservatório independente por uma pequena válvula-esfera; (2) um fluxômetro com orifício a jusante do vaso coalescedor, que inclui flanges, placa do orifício e medidor de pressão diferencial; (3) uma válvula de agulha para regular o fluxo de gás pelo vaso coalescedor; (4) duas entradas de coleta de amostra a jusante e a montante do vaso coalescedor, para os quais dois kits de teste de gás podem ser conectados simultaneamente visando analisar a qualidade do gás influente e efluente; e (5) duas mangueiras flexíveis de aço inoxidável conectando o kit de teste à linha de gás principal e à linha de descarga.
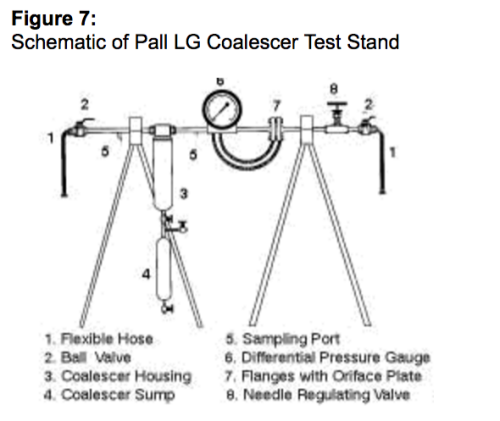
Procedimento do teste
Antes de ir ao local para um teste de campo, faz-se contato com a planta para se obter as condições do sistema (pressão, temperatura, vazão do gás, tipo de gás e, se possível, a concentração de líquido no fluxo de gás. Com base nessas informações, uma placa com orifício é selecionada para medir as vazões do gás na faixa indicada. O orifício também é selecionado para minimizar a queda de pressão para que a condensação de gás e a formação de hidrato não sejam induzidas
Após instalar o kit de teste no fluxo lateral na linha, a vazão será ajustada abaixo da vazão crítica, de modo que não haja reentrada. Assim que o cartucho coalescedor ficar saturado, as membranas do teste serão inseridas nos gabaritos de teste a jusante e a montante do vaso coalescedor, o reservatório será esvaziado de qualquer líquido que possa ter se acumulado durante o período de saturação do cartucho e o teste real começará.
Ao final do teste, o volume de líquido acumulado no reservatório é medido e coletado em um frasco de amostra para posterior análise laboratorial. As membranas do teste também serão coletadas para determinar a quantidade de sólidos suspensos no gás e para identificação qualitativa dos contaminantes sólidos. A concentração de aerossol líquido será determinada pela quantidade de líquido coalescido e a quantidade de amostra de gás coletada.
Resultados do teste de campo
Os resultados dos testes de campo nos 49 fluxos de gás (gás natural, dióxido de carbono, hidrogênio e gás combustível) nas plantas de processamento de gás e nas refinarias mostram quantidades significativas de líquido presentes na maioria dos fluxos de gás. A Figura 8 resume esses resultados dos testes. Dos 49 fluxos de gás testados, mais de 85% (43 de 49 testes) continham concentração de líquidos superiores a 1 ppmw. Essa concentração de líquido pode resultar em problemas significativos em equipamentos rotativos e pode contribuir com operações de processo ruins em uma unidade de contato de amina.
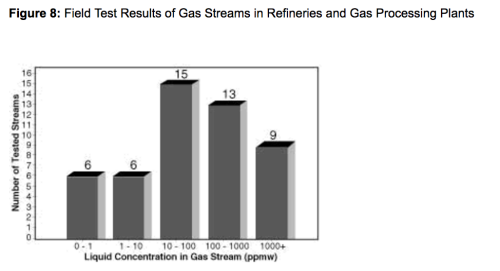
Conclusões
1. Selecionar tecnologias de separação gás/líquido exige não apenas conhecimento das condições do processo, mas conhecimento das características dos contaminantes líquidos. A seleção deve ser feita com base no tamanho das gotículas, concentração e se o líquido tem tendências de formação de cera ou incrustação.
2. Através de uma análise de dados de campo, foi demonstrado que devido à presença de gotículas de líquido muito finas (abaixo de 1 mícron) na maioria dos processos de gás, coalescedores líquido/gás de alta eficiência devem ser recomendados sempre que altas taxas de recuperação são necessárias para proteger equipamentos a jusante ou para recuperar líquidos valiosos.
3. O dimensionamento e o design de um coalescedor são extremamente importantes. Uma vez que um coalescedor é desafiado com muito líquido, seja por causa de concentrações excessivas de aerossol ou grandes taxas de fluxo de gás, sua eficiência diminuirá rapidamente
4. O teste de Eficiência de Separação de Aerossóis Líquidos (LASE) é um teste de desempenho significativo de coalescedores líquido/gás, pois permite que os cartuchos coalescentes sejam testados em condições muito semelhantes às condições operacionais reais (elemento saturado, quedas de pressão realistas e propriedades do gás (densidade, viscosidade) .
5. Um tratamento de superfície do meio coalescedor melhoou a drenagem do líquido nos materiais fibrosos e diminuiu em 50% o número de cartuchos necessários para lidar com um determinado fluxo.
6. Testes de campo demonstraram que quantidades significativas de líquidos estão presentes no fluxo de gás em refinarias e plantas de processamento de gás.
Referências
1. C.R. Pauley, D.G. Langston e F. C. Betts, “Redesigned Filters Solve Foaming, Amine Loss Problems at Louisiana Gas Plant,” Oil & Gas Journal, 4 de fev de 1991.
2. Perry’s Chemical Engineers’ Handbook, 6ª Edição, McGraw-Hill, Nova Iorque, 1984, Cap. 18, págs. 48 a 56.
3. Perry’s Chemical Engineers’ Handbook, 6ª Edição, McGraw-Hill, Nova Iorque, 1984, Cap. 18, págs. 48 a 56.
4. K. J. Fewel Jr., J. A. Kean, “Computer Modeling Aids Separator Retrofit, ”Oil & Gas Journal, 6 de julho de 1992.
5. A. K. Coker, “Computer Program Enhances Guidelines for Gas-Liquid Separation Designs”, Oil & Gas Journal, 10 de maio de 1993.
6. Perry’s Chemical Engineers’ Handbook, 6ª Edição, McGraw-Hill, Nova Iorque, 1984, Cap. 18, págs. 48 a 56.
7. K. J. Fewel Jr., J. A. Kean, “Computer Modeling Aids Separator Retrofit, ”Oil & Gas Journal, 6 de julho de 1992.
8. Perry’s Chemical Engineers’ Handbook, 6ª Edição, McGraw-Hill, Nova Iorque, 1984, Cap. 18, págs. 48 a 56.
9. C. A. G. Regan and M. Baker, “A Novel Separator/Scrubber Design Program - The Impact of Upstream and Downstream Equipment on Separation Performance,” Documento técnico apresentado na 9ª Reunião Continental da Associação de Processamento de Gás, Capítulo europeu, 14 e 15 de maio de 1992.
10. Perry’s Chemical Engineers’ Handbook, 6ª Edição, McGraw-Hill, Nova Iorque, 1984, Cap. 18, págs. 48 a 56.
11. C. Dickenson, “Filters and Filtration Handbook,” 3ª Edição, Elsevier Adv. Tech, Oxford, 1992, págs. 44 a 47.
12. K. Williamson, S. Tousi e R. Hashemi, “Recent Developments in Performance Rating of Gas/Liquid Coalescer,” Documento técnico apresnetado na 1ª Reunião Anual da Sociedade Americana de Filtração, 21 a 25 de março, Ocean City, MD.
13. J. D. Miller, E. E. Koslow, K. W. Williamson, Patente EUA 4.676.807, 30 de junho de 1987; id., Patente EUA 4.759.782, 26 de julho de 1988.
Nossos produtos
Liderando o setor com soluções e produtos adaptados às necessidades dos clientes.