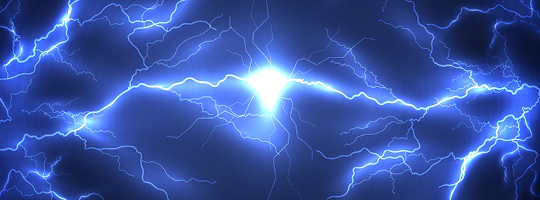
Understanding varnish contamination in rotating equipment – and how to solve it effectively
What is varnish in oil?
Varnish is an insoluble film deposit that forms on surfaces inside turbine lubrication systems like pipes, tanks, bearings, heat exchangers, and servo-valves. It appears as a sticky substance in the oil, or on the metal surface of lubrication systems. Under normal operating conditions, all turbine oils generate varnish materials, but the rate is higher under severe or unusual operating conditions. In most cases, varnish forms due to extreme temperatures. Higher operating temperatures accelerate the oxidation of the oil, making its effectiveness a challenge.
Varnish challenges in turbine lube systems
Oil has limited solvency for varnish. Most of the varnish in a lube system is in the form of deposits A portion of the varnish is suspended in the oil, and as the oil is cleared, more varnish dissolves. Varnish deposits cause:
- Restriction and sticking of servo valves
- Bearing deposits: reducing oil film thickness and clearances
- Increased water rates of bearings
- Reduced cool efficiency in heat exchangers
Consequently, replacement of contaminated vales and chemical cleans and flushes are costly. The downtime and loss of production represent a large share of the costs associated with poor varnish control in turbine installations.
Guidelines to measuring varnish in oil
It is not possible to control what we cannot measure. However, there are guidelines for varnish identification:
- Dark-colored oil
- Oil sample with an acidic odor
- Presence of non-particulate silt on a 0,8 or 1,2 µ test membrane
- High operating temperature or hot spots in the system (>80°C)
- Servo valve failure, last chance filter clogging in a cold pilot line
- Premature filter clogging
- Sticky residue on the system components
If any of these indicators are present, it is highly recommended to perform laboratory analyses.
Solving the challenge of varnish in oil - setting removal targets
Measurement of varnish potential does not indicate the actual amount of varnish deposited on the surfaces of components. It measures varnish precursors in the oil. A system is varnish-free when varnish deposits have disappeared and not necessarily when varnish potential is down. Removing varnish materials from the oil displaces the solvency equilibrium in the oil, forcing it to re-dissolve in the fluid, and then it's eliminated by varnish removal units.
Varnish precursor measurements must be consistently low for an extended period to be free of varnish. Clean-up time depends on the removal efficiency, the number of deposits already present in the system, and the solvency of the varnish.
How effective are Traditional Varnish Removal Methods?
There are several methods used to remove varnish with varying levels of success. The electrostatic method involves exposing the oil to an electrical field which causes varnish particles to agglomerate. However, there the results of this are mixed. The chemical flush method works by softening varnish deposits which are then lifted by circulating flushing fluid. However, this process can be an expensive and time-intensive process, as it can take several hours or days depending on the system.
Pall Recommendation: The Adsorption method
The adsorption method utilizes a large surface area and high void volume. Combined with a low flow rate, adsorption allows for proper residence time for adsorption. The filtration medium traps varnish precursors through weak molecular forces. Constructed of cellulose fibers, it creates a porous matrix for additive integration, providing strength and flexibility.
Using an adsorption method like Pall’s VRF (Varnish Removal Filter) system has many advantages over the other methods. Field experience with this system on gas turbines showed a rapid and stable reduction in varnish potential rating (VPR), below the recommended levels. A combination of Pall anti-static filter media on the main lube line and CRF skid offline eliminates varnish-related problems.
Performance
Field experience with Pall VRF on gas turbines showed a rapid and stable reduction in varnish potential rating (VPRSM)1 well below the recommended levels. Pall VRF will maintain low varnish potential as the entire system gets cleaned up over time, literally pulling varnish off surfaces for removal. Within a few weeks, a turbine can be free of varnish issues. With the Pall SRT and VRF filters, you can remove existing varnish and prevent varnish from forming.
Contact us to discuss varnish removal, or watch our on-demand webinar to learn more about the causes, effects, and remedies for varnish removal.
- Category
- Author
- Sort By