Midstream Oil & Gas Filtration and Separation
Essential for the Removal of Solid Contaminants Prior to Pipeline Transportation
Minimize Downtime and Optimize Your Oil & Gas Midstream Business
The reliability of midstream oil and gas processes is paramount to keeping both upstream production and downstream refining facilities online. Failure to effectively separate and filter produced fluids and supporting fluid systems throughout the transportation and processing operations can result in lengthy and costly downtime.
Midstream filtration and separation supporting fluid systems such as compressor lubricants and solvent recycle systems is essential to the removal of solid contaminants. With our solutions you will minimize equipment downtime, extend the life of capital equipment, and improve the efficiency of other processing operations in your oil gas facility.
The midstream operations rely on fluid separation systems. The separation of produced water from liquid hydrocarbons and reservoir gases is necessary to preserving pipeline integrity and the life of equipment further downstream. Our advanced separation and filtration technologies deliver premium filtration performance with unmatched reliability and reduced maintenance frequency for an efficient streamlined operation.
While it is crucial to separate and filter produced oil, gas, and water to preserve pipelines and downstream equipment, other fluids such as lubricants and solvents are equally important for the fluid transfer and processing operations. To preserve the life of compressors and other downstream equipment that are negatively affected by contaminated fluid streams, further downstream filtration is required to continually purify fluid streams.
Beyond the initial separation and filtration of produced fluids, further filtration is required downstream to purify fluid streams. This is necessary to preserve the life of compressors and other downstream equipment that are negatively affected by contaminated fluid streams. Dehydration and removal of acid gases are also critical in midstream processing operations to help meet pipeline quality specifications. These processes rely on solvents such as amines and glycol to remove water and hydrogen sulfide from produced gas that can corrode pipelines and downstream process equipment as well as present substantial safety risks to personnel.
As the global leader in advanced filtration technologies, Pall Corporation delivers proven and complete filtration solutions for all aspects of midstream oil and gas operations. Our filtration and separation technologies throughout the midstream oil and gas processes deliver a complete solution that enhances performance, increases process reliability, reduces maintenance frequency and downtime, and lowers operating costs for significantly improved business performance.
Explore our midstream oil and gas filtration and separation solutions for gas transmission, gas processing and Liquefied Natural Gas (LNG) production.
Unmatched Reliability
Pall’s industry leading coalescers deliver premium gas/liquid and liquid/liquid separation with unmatched reliability to increase process efficiency.
Literature Library
MIDSTREAM Products
For more information about our range of products, explore our product catalog.
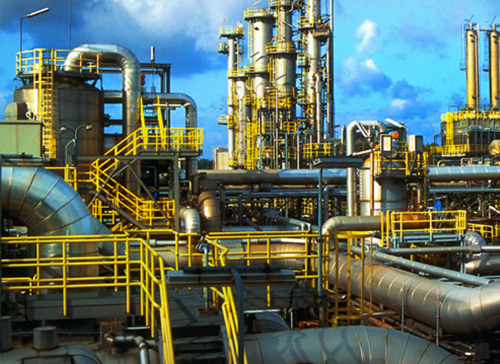
Acid Gas Sweetening
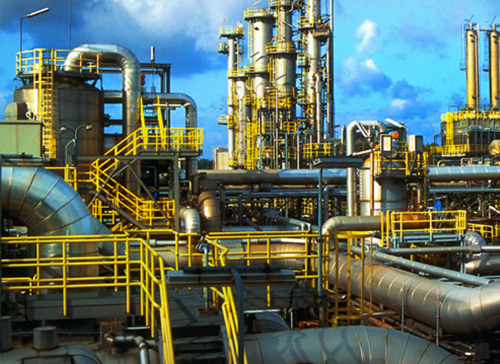
Condensate Stabilization/Fractionation
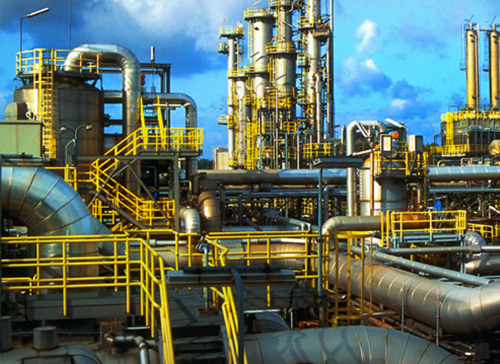
Midstream Black Powder
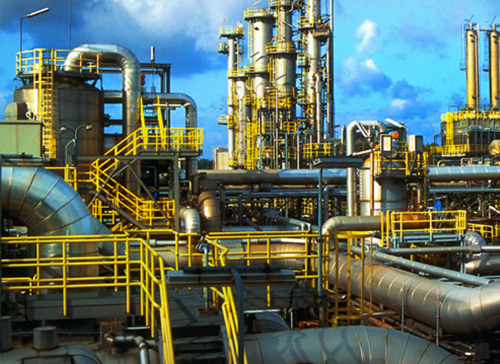
Condensate Pipeline Dewatering
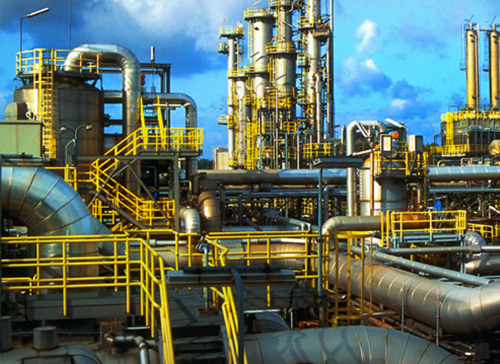
Glycol Dehydration
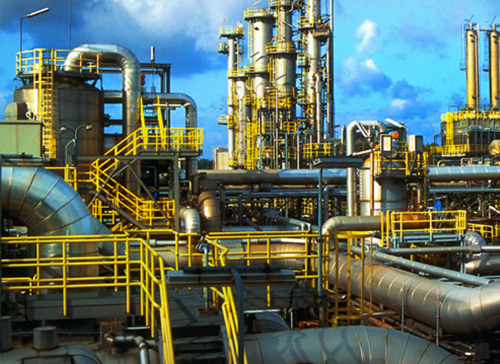
Mercury Removal Unit (MRU)
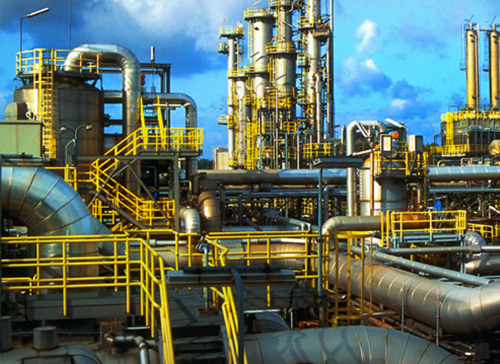
Adsorbent Dehydration
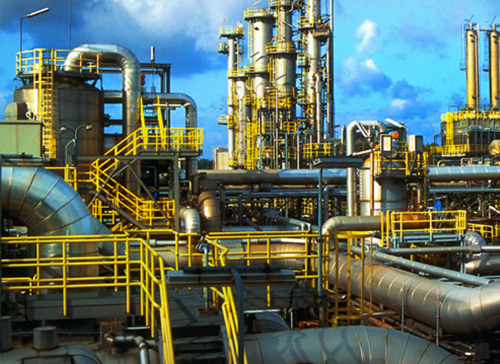