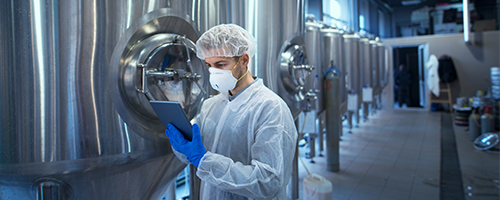
9 Essential Attributes of Sterilizing-Grade Air and Gas Cartridge Filters
November, 2024
Sterilizing-grade air and gas cartridge filters are crucial to maintaining the integrity of critical applications in the food and beverage industry. These specialized filters are engineered to effectively remove microorganisms from air or other gases like nitrogen or carbon dioxide. Microbial contamination negatively affects product quality, leading to issues such as sensory and nutrient quality degradation, reduced shelf life, spoilage, or even risks to human health. In some cases, unwanted microbial and bacteriophage contamination can lower process yield.
Though much emphasis is placed on microbial retention, several other essential attributes of sterilizing-grade air and gas filters play a crucial role in successful filtration. Below are the nine areas that sterilizing-grade filters must feature.
Microbial Retention
Microbial retention is the most crucial attribute of sterilizing-grade air filters. If the required sterility in a critical application cannot be achieved, the main goal of filtration is compromised.
The FDA requires sterilizing-grade air filters to be validated for consistent retention of Brevundimonas diminuta (ATCC 19146) at a concentration of 107cfu/cm², ensuring sterile effluent. This 0.3 µm microorganism necessitates thorough microbial validation during filter development and production.
Validation methods include liquid or aerosol challenge testing, influencing filtration results. Manufacturers may demonstrate effectiveness against bacterial spores and conduct long-term aerosol challenges. Besides the basic bacterial challenge test, additional validation can show the filters' suitability, such as retention of bacterial spores and aerosol bacteriophage removal.
Hydrophobicity
Hydrophobicity is a physical property that refers to a materials lack of affinity for water. A hydrophobic material repels moisture rather than adsorbs it. Materials vary in hydrophobicity, measured in dynes/cm, indicating their critical surface tension.
High hydrophobicity is essential for air filters, as low hydrophobicity can lead to moisture absorption, reduce airflow, and potentially cause filter collapse under pressure. Hydrophobic filters also dry faster after steam sterilization. PTFE media provides the best long-term hydrophobicity, with some sterilizing filters using either PTFE media or treatments. Filters must retain hydrophobicity throughout their service life, as partial wetting in compressed air systems can create "hydrophilic spots," compromising filtration effectiveness.
Low Resistance to Airflow
Low resistance to airflow is a critical quality in sterilizing-grade air filters, enabling more compact installations. In high-airflow applications, the design of the filter housing—including inlet and outlet connections—becomes crucial for maintaining airflow rates and minimizing pressure drops, which can save energy in compressed air systems.
The porosity of the filter media, or its open area, allows for airflow. Higher porosity results in lower resistance, but larger filter areas don't always equate to increased airflow. Furthermore, the thickness of the filter fibers influences porosity: thinner fibers yield greater porosity.
Robustness
Sterilizing-grade air filters undergo repeated in-situ steam sterilization, requiring robust design to endure >100-200 cycles lasting 0.5-1 hour without losing retention performance. The primary stressor is steam sterilization, which can soften the filter media due to high temperatures, causing stress from varying expansion rates of materials. Additionally, high differential pressure during operation must be validated to ensure maximum resistance. Users must adhere to manufacturer limits regarding steaming frequency, duration, differential pressures, and temperatures. Filter durability relies on the design and materials of the media, support layers, hardware, and sealing methods used in construction.
Suitable Geometry
Sterilizing-grade air filters should be single-open-end designs with a twist-lock adaptor, double bayonet design, two O-rings, and an internal adaptor ring for stability. A tight seal prevents unfiltered air bypass, ensuring good physical stability during operation. Threaded connections in the adaptor are discouraged for hygienic reasons.
Integrity Testing
Microbial retention validation is a destructive test, so a non-destructive integrity test is crucial for verifying the performance of sterilizing-grade air filters. Manufacturers establish a pass/fail value for these tests that correlates with microbial removal efficiency, including a safety factor. Integrity tests can detect even minor damage in the filter's medium, seal, and hardware, which may not be visible. Ideally, this testing should occur before and after production to minimize batch failure risks.
Application Compatibility
Sterilizing-grade air filters can be exposed to air for months or even years. Their materials must be validated for oxidation resistance based on expected duration, temperatures, and compatibility with chemicals like hydrogen peroxide. Degradation from material incompatibility can compromise filtration integrity, often indicated by a failed integrity test. Severe degradation may manifest as white powder from the filter media, support, and drainage layers.
Absence of Toxic Substances
Filter construction materials must not release toxic substances into the product or onto surfaces that contact it. These materials should also comply with national and international regulations for direct or indirect food contact use.
Documented Validation, Quality and Traceability
Filter manufacturers use a "Validation Guide" or "Technical Performance Document" to support performance claims. This document outlines tested attributes, configurations, methodologies, and results.
Each filter should undergo an integrity test before shipping, and its traceability should be via serial numbering. A robust quality assurance program is crucial for delivering consistent, high-quality products that meet customer expectations.
Meeting all 9 attributes: Emflon® PFR Filter Cartridges
Pall’s Emflon family of validated PTFE filters meets industry demand for the highest level of sterility assurance. Emflon membrane filters fulfil a microbial liquid bacteria challenge validation that meets requirements to remove at ≥107 cfu/cm2 effective filtration area, according to ASTM Method 838-05, providing sterile effluent according to FDA Guidelines (2004). To learn more visit here.
Subscribe to our blog to stay up-to-date on the latest food and beverage insights and trends
- Category
- Author
- Sort By