コンプレッサー、バーナーチップ、アミンおよびグリコールユニット、モレキュラーシーブ、水銀ガードベッドの保護用
ガスから液体と固体を除去することは、精製およびガス処理アプリケーションで非常に重要です。これらの汚染物質を効果的に除去することで、コンプレッサー、タービン、バーナーなどの下流設備でのコスト発生や休止期間を防ぐことができます。さらに、炭化水素と固体汚染物質は、アミン分離膜コンタクタータワーで泡立ちを誘発する可能性があり、触媒プロセスでの早期の触媒交換に繋がる可能性があります。シリンダーを潤滑するためにオイルを使用するコンプレッサーでは、潤滑油が排出ガスに入り込み、下流で汚染を引き起こすことがよくあります。熱交換器に堆積した炭化水素の薄膜は、厚くなり、コークス化して、熱伝達効率を低下させ、エネルギー消費を増加させ、ホットスポットやリークのリスクを生み出します。
液体ガスと固体ガスの分離には、いくつかの技術が利用できます。この記事では、最初に次の気液分離技術の選択基準を紹介します。
- 重力セパレーター
- 遠心分離機
- フィルターベーンセパレーター
- ミスト除去パッド
- 液体/気体コアレッサー
次に、液体/ガス合体技術を使用して、ガスから微細なエアロゾルを分離することに焦点を当てます。
除去メカニズム
特定の技術を評価する前に、固体ガスと液体ガスの分離に使用されるメカニズムを理解することが重要です。これらは4つの異なるカテゴリーに分けることができます²。最初に最も理解しやすいのは重力沈降です。これは、液滴または粒子の重量(つまり重力)が、流れるガスによって生成される抗力を超えたときに発生します。
関連するより効率的なメカニズムは、遠心力が流れるガスによって生成される抗力を超えるときに発生する遠心分離です。遠心力は重力の数倍になることがあります。
3番目の固体および液体ガス分離メカニズムは慣性衝突と呼ばれ、ガスがメディアを通過するときに発生します。この場合、ガス流はこれらのメディアの周りの曲がりくねった経路をたどりますが、固体または液滴はよりまっすぐな経路をたどる傾向があります。これが発生すると、液滴または粒子は速度を失う、または合体をして、最終的には容器の底に落ちるか、繊維媒体に閉じ込められたままになります。
そして最後に、4番目の液体と固体のガス分離プロセスが非常に小さいエアロゾル(0.1 µm未満)で発生します。ブラウン運動と呼ばれるこのメカニズムは、小さなエアロゾルがガス分子と衝突したときに発生します。これらの衝突により、エアロゾルがバリア周辺の流体流路から外れ、エアロゾルが繊維表面に衝突して除去される可能性が高くなります³。
このプロセスを通して、液滴と粒子のサイズ単位はミクロンになります。1ミクロンは1/1000ミリメートルまたは39/1,000,000インチです。図2は、さまざまな材料のサイズをミクロン単位で示しています。
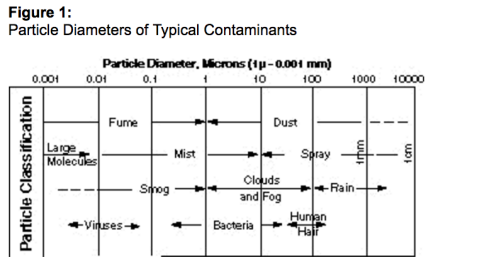
除去メカニズム
特定の技術を評価する前に、固体ガスと液体ガスの分離に使用されるメカニズムを理解することが重要です。これらは4つの異なるカテゴリーに分けることができます²。最初に最も理解しやすいのは重力沈降です。これは、液滴または粒子の重量(つまり重力)が、流れるガスによって生成される抗力を超えたときに発生します。
関連するより効率的なメカニズムは、遠心力が流れるガスによって生成される抗力を超えるときに発生する遠心分離です。遠心力は重力の数倍になることがあります。
3番目の固体および液体ガス分離メカニズムは慣性衝突と呼ばれ、ガスがメディアを通過するときに発生します。この場合、ガス流はこれらのメディアの周りの曲がりくねった経路をたどりますが、固体または液滴はよりまっすぐな経路をたどる傾向があります。これが発生すると、液滴または粒子は速度を失う、または合体をして、最終的には容器の底に落ちるか、繊維媒体に閉じ込められたままになります。
そして最後に、4番目の液体と固体のガス分離プロセスが非常に小さいエアロゾル(0.1 µm未満)で発生します。ブラウン運動と呼ばれるこのメカニズムは、小さなエアロゾルがガス分子と衝突したときに発生します。これらの衝突により、エアロゾルがバリア周辺の流体流路から外れ、エアロゾルが繊維表面に衝突して除去される可能性が高くなります³。
このプロセスを通して、液滴と粒子のサイズ単位はミクロンになります。1ミクロンは1/1000ミリメートルまたは39/1,000,000インチです。図2は、さまざまな材料のサイズをミクロン単位で示しています。
図1は、さまざまな材料のサイズをミクロン単位で示しています。
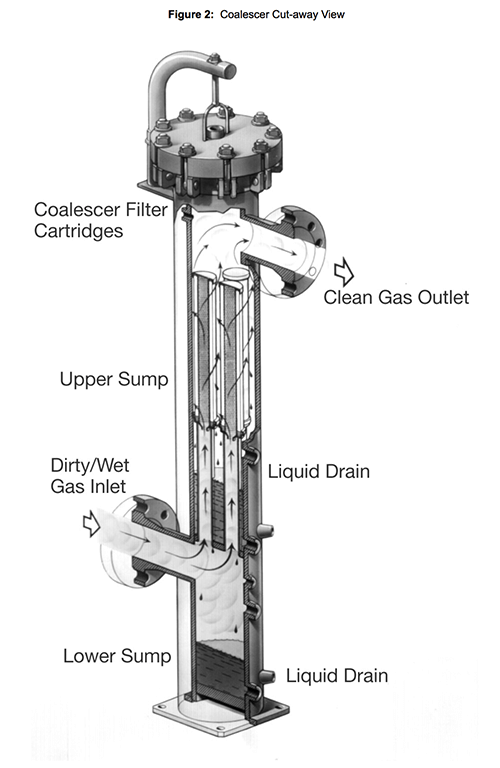
液体/ガス分離技術
重力セパレーター
重力分離器またはノックアウトドラムでは、重力が分離を制御します。ガス速度が遅く、容器のサイズが大きいほど、液体/ガスの分離が効率的になります。沈降を達成するために必要な大きな容器サイズのため、重力分離器は、300ミクロン⁴未満の液滴を除去するように設計されることはめったにありません。ノックアウトドラムは通常、バルク分離または第1段階目のスクラバーとして使用されます。ノックアウトドラムは、救援システムやファウリングサービスのように船内を最小限に抑える必要がある場合にも役立ちます⁵。高い分離効率が必要な場合、重力分離器は推奨されません。
遠心分離機
遠心分離機またはサイクロン分離機では、遠心力が重力の数倍の力でエアロゾルに作用する可能性があります。一般に、サイクロン分離器は、直径100 µmを超えるエアロゾルを除去するために使用され、適切なサイズのサイクロンは、10 µmという低いエアロゾルの除去を実現できます。10µm⁶未満のミスト粒子では、サイクロンの除去効率は非常に低くなります。ワックス状またはコークス化材料には、サイクロンとノックアウトドラムの両方をお勧めします。
ミスト除去パッド
ミスト除去パッドの固体/液体ガス分離メカニズムは、慣性衝突です。通常、繊維またはニットメッシュで構成されるミスト除去パッドは、1〜5ミクロンまでの液滴を除去できますが、液体の再飛散を防ぐために低速で操作する必要があるため、液滴を含む容器は比較的大きくなります。
ベーンセパレーター
ベーンセパレーターは、容器内の一連のバッフルまたはプレートです。分離を再び制御するメカニズムは慣性衝突です。ベーンセパレーターは、除去効率のために質量速度に敏感ですが、主に、より効果的な液体排水が液体の再飛散を低減するため、ミスト除去パッドよりも高速で動作できます。しかし、曲がりくねった流路を構成するプレート間の経路が比較的大きいため、ベーンセパレーターは比較的大きな液滴サイズ(10ミクロン以上)しか除去できません。多くの場合、ベーンセパレーターは、ガス速度が設計速度⁷を超えたときにミストエリミネーターパッド容器を改造するために使用されます。
液体/気体コアレッサー
液体/ガスコアレッサーカートリッジは、ミスト除去パッドとベーンセパレーターの両方の機能を組み合わせていますが、通常、バルク液体の除去には指定されていません。バルク液体システムでは、高効率のコアレッサーは通常、ノックアウトドラムまたはセパレーターの下流に配置されます。ガスは、液体の排出を促進するために外面を包む、結合した繊維上を通って流れます(下の図2を参照)。コアレッサーカートリッジは、0.1ミクロンまでの液滴を捕捉できます。適切に設計およびサイズ設定されている場合、繊維からの合体液滴の排出により、液体の再飛散やアセンブリ全体の圧力降下が増加する懸念がなく、ミスト除去パッドおよびベーンセパレーターの場合よりもはるかに高いガス速度が可能になります。
表1は、これらの各テクノロジーを要約し、適切に選択するためのガイドラインを示しています。ご覧のとおり、6 µm未満の非常に微細なエアロゾルを含むシステムでは、コアレッサーを選択する必要があります。ガスから非常に細かいエアロゾルを除去すると、コンプレッサーシステムの経済性、信頼性、およびメンテナンスに大きなメリットがあります。
表1は、これらの各テクノロジーを要約し、適切に選択するためのガイドラインを示しています。ご覧のとおり、6 µm未満の非常に微細なエアロゾルを含むシステムでは、コアレッサーを選択する必要があります。ガスから非常に細かいエアロゾルを除去すると、コンプレッサーシステムの経済性、信頼性、およびメンテナンスに大きなメリットがあります。
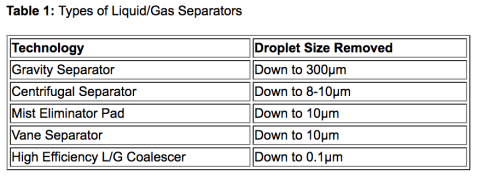
微細エアロゾルの形成
非常に微細な液体エアロゾルがガス流に入るには、いくつかの方法があります。
- 飽和蒸気からの凝縮、
- 噴霧(流量制限によるスプレー効果)、および
- 液体の再飛散。8
天然ガス流中のエアロゾルサイズ分布に関する最近の研究では、チョークバルブやその他の制限が存在する場合⁹または蒸気が露点にある場合は常に、5ミクロン未満のかなりの量の液滴が標準であることが確認されています¹⁰。図4に示す測定は、ベーンセパレーター(重力セパレーターと水平フィルターバリアの組み合わせで、ミスト除去パッドに相当)の下流でサンプリングされた天然ガスストリーム中の液体エアロゾルの濃度を決定するために実行されました。結果は、多くの場合、液滴が小さすぎてこれらの分離装置でトラップできないため、大量のエアロゾルがこのタイプの分離器を通過する可能性があることを示しています。結果として、
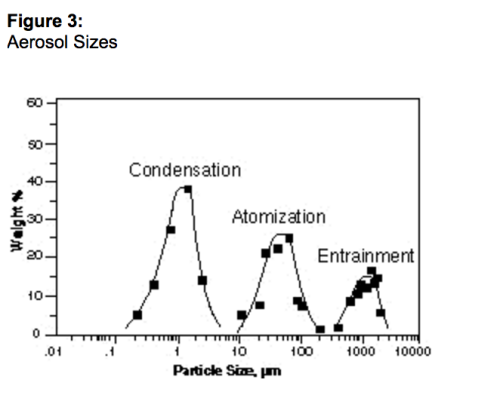
評価/サイジング
コアレッサーは、微粒子のろ過とガス流からの液体エアロゾルの合体の両方を実行するという点で、フィルターとは異なることに注意することが重要です。液体の除去に関連するコアレッサーのサイジングと評価の基準は、コアレッサーの最終的なパフォーマンスにとって非常に重要です。小さすぎるコアレッサーは、継続的な液体の再飛散、非常に低い液体ガス分離効率をもたらし、プロセスの変更に対して脆弱になります。コアレッサーのサイジングの重要な性質を図5に示します。これは、コアレッサーが液体の量が多すぎると(ガス流中のエアロゾル濃度が高いため、またはガス流量が多いため)、コアレッサーの性能が急速に低下する可能性があることを示しています。
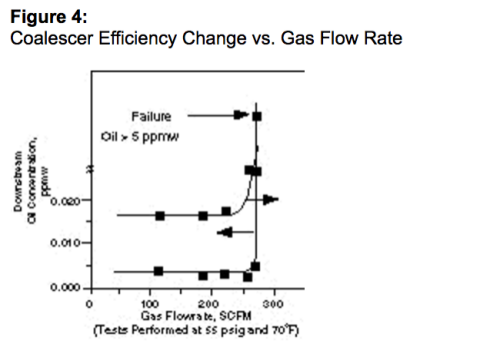
コアレッサーの性能検証の従来の手段は、DOP(ジオクチルフタレート)テスト¹¹です。この試験では、直径0.3 µmの単分散エアロゾルが、制御された条件下でのDOP蒸気の凝縮によって連続的に生成されます。エアロゾルの生成が安定すると(一定の粒子サイズとエアロゾル濃度)、DOPの濃度が光散乱光度計によってコアレッサーの上流と下流で測定されます。結果は、使用された流量でのDOP浸透のパーセントとして表されます。
DOPテストのいくつかの注意点は次のとおりです¹²1
1. テストはドライまたは不飽和カートリッジで実行されます。ドライカートリッジは、本質的にスポンジのように機能し、通過する液体を吸収します。DOPテストで測定されないのは、液体がコアレッサー媒体を飽和させ、下流に再同伴される可能性がある場合に、コアレッサーが液体を保持する能力です。
2. これは2番目の欠点につながります。アセンブリ全体で測定された圧力降下は、飽和要素全体の実際の圧力降下と比較すると過小評価されています。飽和DPは、クリーンDPの約2〜4倍です。
3. テストは、ガスの特性(密度と粘度)が実際の動作圧力で一般的なものとは大きく異なる部分真空下で実行されます。DOPテスト条件は、コアレッサー要素の効率を誇張する傾向があります。
DOPテストの欠点を回避するために、ポールは液体エアロゾル分離効率(LASE)テストを開発しました。この試験は、製油所やガス処理プラントで見られる条件により類似した条件下で、圧縮ガス流のコアレッサー性能を測定することのみを目的として開発されました。このテストに使用されたシステムは、図6に示されています。
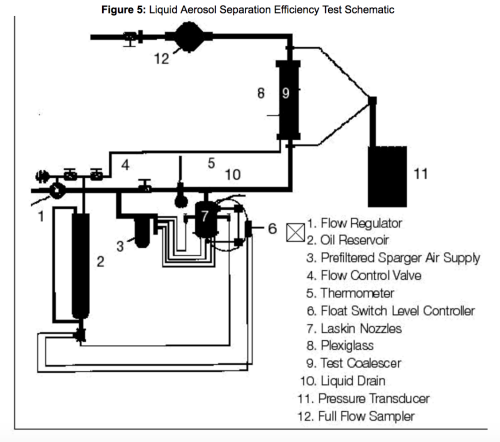
LASEテストは次の点でDOPテストと異なります
1. より正確で意味のある効率の測定値を提供します。DOP効率は、基本的に、0.3 µmのフタル酸ジオクチル液滴の何パーセントが乾式コアレッサーによって除去されるかを示します。LASEテストは、コアレッサーの下流のガスに含まれる汚染物質のppmwを示します。言い換えると、LASEテストでわかるのは、下流の機器がどれだけの汚染物質にさらされるかということです。
2. DOPは、ガス処理または精製ガスストリームでは一般的に遭遇しない液体であるDOPの単分散(つまり同じサイズ)の液滴を使用します。LASEテストでは、液滴サイズが0.1〜0.9 µmの潤滑油を使用します。
3. LASEテストは、飽和カートリッジで実行され、陽圧下で実行されることにより、プロセス条件をより厳密にシミュレートします。
表3に、DOPテストとLASEテストの比較を示します。
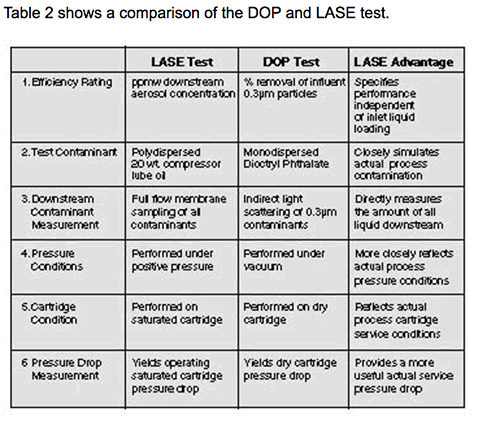
デザインとそのサイジングへの影響
コアレッサーの設計を改善する目的は、液体の再飛散を防ぎながら効率を最大化することです。再飛散は、コアレッサー要素に蓄積された液滴が出口ガスによって運び去られるときに発生します。これは、放出ガスの速度、または環状速度が排出液滴の重力を超える場合に発生します。
正しいコアレッサーのサイズ設定の重要性については、前に説明しました。コアレッサーの設計とサイズ設定では、次のパラメーターを考慮する必要があります。
- メディアを通過するガス速度、
- 媒体を出るガスの環状速度、
- 入口ガス中の固体および液体エアロゾル濃度、および
- コアレッサーの排水性
入口エアロゾル濃度を除いて、これらの各要因を制御することができます。一定のガス流量では、媒体の細孔構造の粗さを変更するか、使用するカートリッジの数を増減することにより、媒体の速度を制御できます。ただし、媒体が粗いほど、コアレッサーが液体を除去する効率が低下します。
一定のガス流量では、容器のサイズまたはカートリッジ間のスペースを増減することにより、ガスの排出速度を制御できます。
排水は、低表面エネルギーの合体材料を選択するか、合体する液体の表面張力よりも低い値に媒体の表面エネルギーを下げる化学物質で合体媒体を処理することによって改善できます¹³。表面エネルギーの低い材料を使用すると、液体が濾材を濡らすのを防ぎ、媒体の繊維に沿った液体の排出を促進します。繊維状材料に合体した液体は、気体によって押し出されて再飛散する細孔に蓄積することなく、繊維のネットワークを通って急速に落下します。図6は、化学処理がコアレッサーに与える影響を示しています。これは、化学的に処理されたカートリッジの最大流量が、処理されていない同様のカートリッジの最大流量の3倍以上であることを示しています。
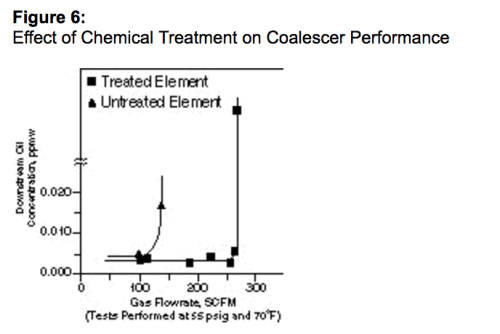
これらの設計パラメータから、非常に微細な細孔を備えた多数のカートリッジを備えた大きなハウジングは、ガス流で遭遇する可能性のある液体の問題を容易に排除すると結論付けることができます。そのようなハウジングに関連するコストは非常に高いです。容器のサイズとカートリッジの量が減ると、再飛散の可能性が減り、除去効率が低下します。さらに、アセンブリのサイズが小さくなると、圧力損失が大きくなり、運用コストが増加する可能性があります。したがって、最適化が必要です。コアレッサーアセンブリを評価するときは、アセンブリのサイズを決定するときに、これらのパラメーターがすべて考慮されていることを確認してください。コ+C17アレッサーは、ノックアウトドラムまたは他のセパレーターと組み合わせて使用するのが最適です。
液体/気体コアレッサーのフィールドテスト
液体を除去する必要があるガス流をフィールドテストすると、次の情報が得られます
1. ガス中の液体の量、
2. 液体を効率的に合体させる能力、
3. 存在する固体粒子状物質の量。
その結果、正確なサンプリングが重要になります。ガス中に存在する液体の量と性質を決定するために、テストコアレッサーカートリッジを通るガス流量を正確に測定することは非常に重要です。
その目的のために、テストキットがサイドストリーム液体/ガスコアレッサーテストを実行するように設計されています。このテストキットを図7に示します。これには次のものが含まれます。(1)小さなボールバルブによって独立したサンプに接続された1つのカートリッジ用のコアレッサーハウジング。(2)フランジ、オリフィスプレート、差圧計を含む、コアレッサーハウジングの下流にあるオリフィス流量計。(3)コアレッサーハウジングを通るガスの流れを調整するためのニードルバルブ。(4)コアレッサーハウジングの上流と下流にある2つのサンプルポート。2つのガステストキットを同時に接続して、流入ガスと流出ガスの品質を分析できます。(5)テストキットをメインガスラインと排出ラインに接続する3本の長いステンレス製ホース。
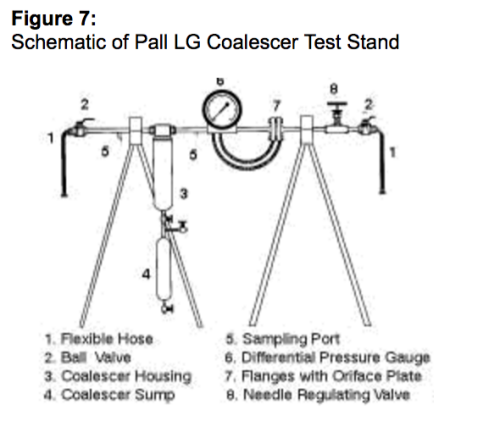
テスト手順
フィールドテストのために現場に行く前に、プラントに連絡してシステム条件(圧力、温度、ガス流量、ガスの種類、および可能であればガス流中の液体濃度)を取得します。この情報に基づいて、示された範囲のガス流量を測定するためにオリフィスプレートが選択されます。オリフィスは、ガスの凝縮とハイドレートの形成が誘発されないように、圧力降下を最小限に抑えるようにも選択されています。
サイドストリームテストキットをオンラインにした後、再飛散しないように、流量を臨界流量未満に調整します。コアレッサーカートリッジが飽和すると、コアレッサーハウジングの上流と下流のテストジグにテストメンブレンが挿入され、カートリッジの飽和期間中に蓄積した可能性のある液体がサンプから空になり、実際のテストが開始されます。
テストの最後に、サンプに蓄積された液体の量が測定され、その後のラボ分析のためにサンプルボトルに収集されます。ガス中に懸濁した固形物の量を測定し、固形物汚染物質を定性的に特定するために、試験膜も収集されます。液体エアロゾル濃度は、合体した液体の量とサンプリングされたガスの量から決定されます。
フィールドテストの結果
ガス処理プラントと製油所の両方で49のガスストリーム(天然ガス、二酸化炭素、水素、燃料ガス)のフィールドテストの結果は、ほとんどのガスストリームにかなりの量の液体が存在することを示しています。図8は、これらのテスト結果をまとめたものです。テストされた49のストリームのうち、85%以上(49のテストのうち43のテスト)の液体濃度が2ppmwを超えていました。この液体の濃度は、回転装置に重大な問題を引き起こす可能性があり、アミン接触装置のプロセス操作が不十分になる原因となる可能性があります。
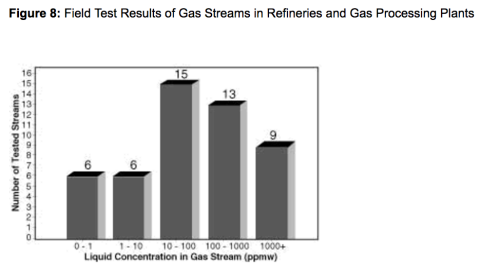
結論
1. 気液分離技術の選択には、プロセス条件の知識だけでなく、液体汚染物質の特性の知識も必要です。液滴のサイズ、濃度、および液体にワックスがけまたは汚れの傾向があるかどうかに基づいて選択する必要があります。
2. フィールドデータの分析を通じて、ほとんどのガスプロセスに非常に細かい液滴(1ミクロン未満)が存在するため、下流を保護するために高い回収率が必要な場合は常に、高効率の液体/ガスコアレッサーを推奨する必要があることが示されました機器または貴重な液体を回収するため。
3. コアレッサーのサイジングと設計は非常に重要です。エアロゾル濃度が高すぎるか、ガス流量が多いために、コアレッサーが液体の量が多すぎると、その効率は急速に低下します。
4. 液体エアロゾル分離効率(LASE)テストは、実際の動作条件(飽和要素、現実的な圧力降下、およびガス特性(密度、
5. コアレッサー媒体の表面処理により、繊維状材料の液体排出が改善され、所定の流れを処理するために必要なカートリッジの数が50%減少しました。
7. フィールドテストでは、製油所およびガス処理プラントのガスストリームにかなりの量の液体が存在することが示されています。
参考文献
1. CR Pauley、DG Langston、およびFC Betts、「再設計されたフィルターは、ルイジアナガスプラントでの泡立ち、アミン損失の問題を解決する」、Oil&Gas Journal、1991年2月4日。
2. Perry's Chemical Engineers'Handbook、6th Edition、McGraw-Hill、New York、1984、Chap。18、pp.48-56。
3. Perry's Chemical Engineers'Handbook、6th Edition、McGraw-Hill、New York、1984、Chap。18、pp.48-56。
4. KJ Fewel Jr.、JA Kean、「Computer Modeling Aids Separator Retrofit」、Oil&Gas Journal、1992年7月6日。
5. AK Coker、「Computer Program EnhancesGuidelines for Gas-Liquid Separation Designs」、Oil&Gas Journal 、1993年5月10日。
6. Perry's Chemical Engineers'Handbook、第6版、McGraw-Hill、ニューヨーク、1984年、Chap。18、pp.48-56。
7. KJ Fewel Jr.、JA Kean、「Computer Modeling Aids Separator Retrofit」、Oil&Gas Journal、1992年7月6日。
8. Perry's Chemical Engineers'Handbook、第6版、McGraw-Hill、ニューヨーク、1984年、Chap。18、pp.48-56。
9. CAGReganおよびM.Baker、「新しい分離器/スクラバー設計プログラム-分離性能に対する上流および下流装置の影響」、ガス処理協会の第9回大陸会議、欧州支部、5月14〜15日に発表された論文、1992。
10. Perry's Chemical Engineers'Handbook、第6版、McGraw-Hill、ニューヨーク、1984年、Chap。18、pp.48-56。
11. C. Dickenson、「Filters and Filtration Handbook」、第3版、ElsevierAdv。Tech、Oxford、1992、pp。44-47。
12. K. Williamson、S。Tousi、およびR. Hashemi、「ガス/液体コアレッサーの性能評価の最近の進展」、3月21〜25日、米国オーシャンシティの第1回米国ろ過学会年次総会で発表された論文。
13. JD Miller、EE Koslow、KW Williamson、米国特許第4,676,807号、1987年6月30日。同上、米国特許第4,759,782号、1988年7月26日。