Stamped for Success
Filtration Solutions Improve Safety and Reliability for Automotive Stamping Presses
Stamping machine press is one of the most commonly used pieces of equipment in automotive manufacturing. In an assembly plant, stamping presses transform sheet metals into complicated part geometries such as hoods, fenders, or door panels. Stamping presses are usually characterized by both Hydraulic and Process filter applications, impacting the reliability of the press, and the quality of the stamped part/surface finish, respectively.
From a production perspective, stamping is a critical stage before E-coating and painting. Before stamping, the sheet metal is usually pre-washed with felt cleaning rollers to remove any solid contaminants from its surface (metal, silica, fibers). When particles remaining on the sheet metal are submitted to a multi-tonne load, they create 'marks' on the stamped surface. These marks usually generate quality defects throughout the pre-treatment, e-coat, or painting phases. The stamping press submits filters to harsh working conditions such as cyclic variations in flow and pressure.
Solutions for maximizing production, reliability, and quality
1. Pre-wash
Depth filtration for stamping process exhibiting a Beta >5,000 filtration efficiency combined with long service life. This filter ensures that the coolant is clean and prevents the nozzles of the low-pressure washing system from clogging. The pre-wash is essential as it helps avoid 'marks' on the sheet metal – the pressure applied by the press on the metal can be a few thousand tons
Suitable products:
Profile® Coreless Filter Elements
Coralon
SUPRAdisc
Why not view our webinar on parts washing?
2. Stamping
Athalon on-line and off-line filters ensure that the particulate contamination resulting from wear mechanisms is maintained under control even in the most severe operating conditions. Usually, on such critical equipment, there are many components very sensitive to particles > 15µm like servo-valves or variable displacement pumps. Athalon stress-resistant filters ensure that the fluid cleanliness level is fully under control to maximize the uptime of the equipment while protecting the critical hydraulic components.
3. Varnish and Water Removal
Removing these elements from the hydraulic fluid, SUPRAdisc™ filter modules, and Purifiers provide the best result. These two items working off-line are incredibly efficient at removing varnish and water. SUPRAdisc lenticular filter modules are made of a cellulose fiber-based medium, combined with resins and additives, while purifiers rely on 'mass transfer under vacuum' technology.
Pall auto stamping filtration technology applied to Hydraulics and Process applications enables Car makers or Tier suppliers to maximize the production coming out of the stamping shop:
1. Increase the equipment reliability and uptime
2. Reduce maintenance costs
3. Reduce defect rates / rework in the paint shop
The Pall Filtration Solutions for Automotive Stamping Press improve the efficiency and safety of the stamping process. For more information, contact a Pall expert today.
Our Products
Leading the Industry with product solutions that fit your customers' needs.
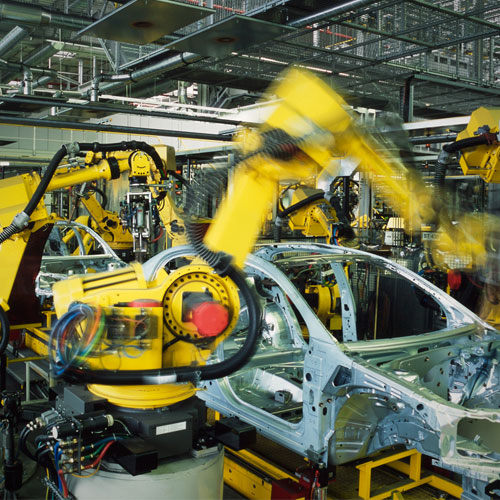
Pre-treatment and E-coat
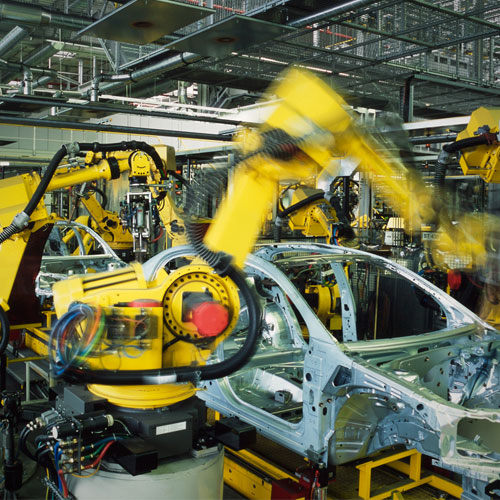