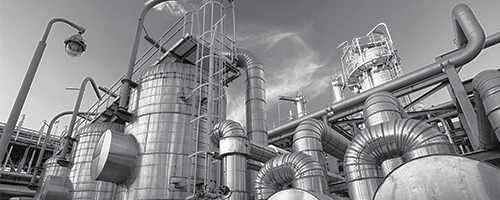
Blog
Optimizing molecular sieve lifetime in natural gas processing
June, 2023
Natural gas is a valuable energy source, and its demand continues to grow globally. As the need for efficient and cost-effective gas processing increases, the optimization of unit processes such as the molecular sieve begins to become increasingly crucial. Molecular sieves are essential components in the overall processing of natural gas and ensure that contamination is removed from the gas stream.
Molecular sieves separate components based on size, adsorbing some while allowing others to pass. Feed gas is typically passed through a bed of adsorbent Zeolite, a crystalline material, used due to its natural formation, high surface area, and small pore size. Molecular sieves (zeolites) are used to dehydrate gas to achieve dew points well below saturation and are effective at removing water vapor to meet water gas specs prior to cryogenic section (avoid freezing) or prior to export. Regeneration is accomplished thermally and will have an associated cost for this heating value.
However, excessive liquid and particulate contamination can significantly increase regeneration frequency, energy consumption, and replacement leading to increased costs. In this blog post, we discuss the top four considerations and best practices for optimizing molecular sieve lifetime and ways to protect against excessive contamination to ensure the lowest operating costs.
1) Understanding the impact of contamination
It is essential to understand the types of contaminates present in the gas stream during processing. Common contaminants include water, hydrocarbons, sulfur compounds, and solid particles. Each contaminant has a different impact, such as pore blockage, deactivation, or chemical reactions. Identifying specific contaminants and their concentration enables the design of effective contamination control strategies.
2) Pre-treatment and Filtration
Proper pretreatment and filtration processes reduce the load of contamination before gas enters the molecular sieve bed. Coalescers, filters, and separators can remove solid particles and liquids actively preventing fouling.
3) Moisture control
Free moisture in natural gas can lead to hydrate formation, ice, corrosion in downstream equipment, and large volumes can affect sieve performance leading to excessive regeneration frequency & fouling. High performance liquid/gas coalescer units should be used to reduce the liquids loading on the sieve bed. Moisture monitoring should also be used to provide real time data for proactive maintenance, ensuring optimal sieve performance.
4) Regular monitoring and maintenance
Implementing a monitoring program helps detect changes in sieve performance or contaminant breakthroughs. Monitoring pressure drop, gas purity, and regeneration cycles allows for timely corrective actions to be taken. Robust scheduled maintenance plans can help prevent performance degradation and significantly lower operating costs.
These four best practices will help you dial in the optimal performance for your gas processing facilities molecular sieve unit. However, it can be difficult to know exactly where to start when looking to implement these actions, Pall corporation is a global leader in contamination control solution for the Oil and Gas industry and will be able to provide support and product recommendations to address issues you may be experiencing with your molecular sieve bed.
For more information visit our website or use the Chat function to speak to our expert team.
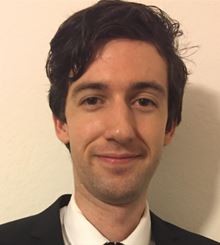
Rory Duncan, Oil and Gas Market Manager
- Category
- Author
- Sort By