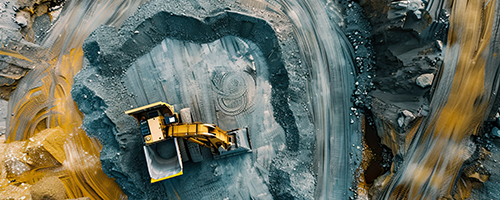
Unlocking the Power of Spodumene: A Key to Sustainable Lithium-ion Batteries
November, 2024
The global demand for clean energy has resulted in an increased search for lithium sources by Li-ion battery manufacturers to meet the ever increasing electric vehicle (EV) demand in the transportation sector. Spodumene, a lithium-bearing ore, plays a crucial role in the EV revolution.
Spodumene is a mineral with the chemical formula LiAlSi2O6, containing 4 to 6% wt. of lithium. Compared to other lithium sources such as lepidolite (2-6 wt. % Li) and petalite (2-3 wt.% Li), spodumene stands out due to its high lithium capacity. It is cost-effective, has a high lithium concentration, and offers a quick transition from mining to the final lithium product compared to brine operations.
Spodumene is the predominant source for extracting lithium from ores. It contributes significantly to the global lithium proven reserves, which currently stand at 26 million tons. Over 145 minerals contain lithium, but only five find utility in commercial lithium extraction: spodumene, lepidolite, petalite, amblygonite, and eucryptite. Among these, spodumene is the most prevalent and yields the largest share of lithium derived from minerals.
From Rock to Power: The Spodumene Extraction
The lithium extraction process involves several stages. The spodumene ore goes through a crushing and roasting process at a high temperature of 2012°F (1100°C) after which it is cooled, milled, and subjected to a secondary roasting process at 482°F (250°C), and acid leaching using sulfuric acid. During this stage, lithium ions displace hydrogen ions in the sulfuric acid, resulting in the formation of lithium sulfate and an insoluble residue.
However, there are challenges in extracting lithium from spodumene, specifically regarding material purity specifications. Lithium-ion batteries manufacturers have strict purity requirements for their source materials. Impurities can lead to poor charging performance, reduced vehicle range, frequent charging needs, problems at colder temperatures, and even battery fires. Improving filtration and separation processes can enhance process reliability, consistency, product quality and yields, and reduce overall operating costs.
Filter | Filtration Value | Separation Product |
---|---|---|
1 | Bulk removal of precipitated salts - high solid concentrations | Filter Press or Centrifuge |
2 | Protect Ion Exchange (IX) resin and crystallizer from carryover solids | 1 - 5 Micron Filter |
3 | Remove trace solids and Ion Exchange resin fi nes before crystallizer | 1 Micron Filter |
4 | Collect Lithium Carbonate product | Filter Press or Centrifuge |
5 | Protect RO filtration unit from fouling. RO used to rinse final product | 10 Micron Filters |
6 | Removal of contaminants from raw water for feed to RO and utility water for other uses including flushing out equipment | 10 - 20 Mircon Filter |
Pall Corporation can assist in optimizing the lithium extraction process. Our filtration technologies can help processors achieve a pure lithium yield of up to 99.5%. Pall Corporation offers various filters for lithium extraction from spodumene, including high-efficiency absolute-rated backwash filters, filter cartridges made of different materials, and technologies targeting dissolved contaminants to improve the purity of lithium products. By utilizing Pall Corporation's filtration solutions, the operation of Lithium Processing Plants can be optimized, leading to more reliable production of battery-grade materials with high purity, improved yield, and lower waste and energy costs.
For a more detailed explanation of lithium extraction from Spodumene, visit our Battery pages and download our application paper, or contact one of our filtration experts directly
Subscribe to our blog to stay up-to-date on the latest insights and trends
- Category
- Author
- Sort By