압축기, 버너 팁, 아민 및 글리콜 장치, 분자체, 수은 보호층 보호용
가스 흐름에서 액체와 고체를 제거하는 것은 정제 및 가스 처리 응용 분야에서 매우 중요합니다. 이러한 오염 물질을 효과적으로 제거하면 압축기, 터빈 및 버너와 같은 다운스트림 장비에서 발생하는 비용이 많이 드는 문제와 가동 중지 시간을 예방할 수 있습니다. 또한 탄화수소 및 고체 오염 물질은 아민 접촉기 타워 에서 거품을 유발할 수 있으며 촉매 공정에서 조기 촉매 교체에 기여할 수 있습니다. 오일을 사용하여 실린더를 윤활하는 압축기에서 윤활유는 종종 배출 가스에 들어가 하류 오염을 유발합니다. 열 교환기에 증착된 탄화수소 박막은 두꺼워지고 코크스화되어 열 전달 효율이 감소하고 에너지 소비가 증가하며 핫스팟 및 누출 위험이 발생합니다.
여러 기술을 사용할 수 있습니다. 액체용 기체 및 고체 기체 분리. 이 기사에서는 먼저 다음과 같은 기체/액체 분리 기술에 대한 선택 기준을 제공합니다.
- 중력 분리기
- 원심 분리기
- 필터 베인 분리기
- 안개 제거 패드
- 액체/가스 코어레서
그런 다음 액체/기체 유착 기술을 사용하여 기체에서 미세한 에어로졸을 분리하는 데 중점을 둡니다.
제거 메커니즘
특정 기술을 평가하기 전에 사용되는 메커니즘을 이해하는 것이 중요합니다. 고체 가스 및 액체 가스 분리. 이는 4가지 범주²로 나눌 수 있습니다. 가장 먼저 이해하기 쉬운 것은 중력 침강이며, 이는 액적 또는 입자의 무게(즉, 중력)가 흐르는 가스에 의해 생성된 항력을 초과할 때 발생합니다.
관련되고 보다 효율적인 메커니즘은 원심력이 흐르는 가스에 의해 생성된 항력을 초과할 때 발생하는 원심 분리입니다. 원심력은 중력보다 몇 배 더 클 수 있습니다.
세 번째 고체 및 액체 가스 분리 메커니즘은 가스가 섬유 및 충돌 장벽과 같은 네트워크를 통과할 때 발생하는 관성 충돌이라고 합니다. 이 경우, 가스 흐름은 이러한 장애물 주위의 구불구불한 경로를 따라가는 반면 고체 또는 액체 방울은 더 직선 경로로 이동하여 이러한 장애물에 영향을 미치는 경향이 있습니다. 일단 이것이 발생하면, 액적 또는 입자는 속도를 잃거나 및/또는 합체되고, 결국 용기 바닥으로 떨어지거나 섬유 매체에 갇힌 채로 남아 있습니다.
그리고 마지막으로 네 번째 액체 및 고체 기체 분리 프로세스 매우 작은 에어로졸(0.1μm 미만)에서 발생합니다. 확산 차단 또는 브라운 운동이라고 하는 이 메커니즘은 작은 에어로졸이 가스 분자와 충돌할 때 발생합니다. 이러한 충돌로 인해 에어로졸이 장벽 주위의 유체 흐름 경로에서 벗어나게 되어 에어로졸이 섬유 표면에 부딪혀 제거될 가능성이 높아집니다³.
이 페이지 전체에서 액적 및 입자 크기에 대한 참조는 미크론 단위입니다. 1미크론은 밀리미터의 1/1000 또는 인치의 39/1,000,000입니다. 그림 1은 다양한 재료의 크기를 미크론 단위로 보여줍니다.

제거 메커니즘
특정 기액 분리를 평가하기 전에 기술을 사용하려면 기체에서 액체와 고체를 제거하는 데 사용되는 메커니즘을 이해하는 것이 중요합니다. 이것들은 네 가지 범주로 나눌 수 있습니다.2 가장 먼저 이해하기 쉬운 것은 중력 침강입니다. 중력 침강은 액적 또는 입자의 무게(즉, 중력)가 흐르는 가스에 의해 생성된 항력을 초과할 때 발생합니다.
관련되고 보다 효율적인 메커니즘은 원심력이 흐르는 가스에 의해 생성된 항력을 초과할 때 발생하는 원심 분리입니다. 원심력은 중력보다 몇 배 더 클 수 있습니다.
세 번째 고체/액체 가스 분리 메커니즘은 가스가 섬유 및 충돌 장벽과 같은 네트워크를 통과할 때 발생하는 관성 충돌이라고 합니다. 이 경우, 가스 흐름은 이러한 장애물 주위의 구불구불한 경로를 따라가는 반면 고체 또는 액체 방울은 더 직선 경로로 이동하여 이러한 장애물에 영향을 미치는 경향이 있습니다. 일단 이것이 발생하면, 액적 또는 입자는 속도를 잃거나 및/또는 합체되고, 결국 용기 바닥으로 떨어지거나 섬유 매체에 갇힌 채로 남아 있습니다.
마지막으로 액체/고체 기체 분리의 네 번째 메커니즘은 매우 작은 에어로졸(0.1μm 미만)에서 발생합니다. 확산 차단 또는 브라운 운동이라고 하는 이 메커니즘은 작은 에어로졸이 가스 분자와 충돌할 때 발생합니다. 이러한 충돌로 인해 에어로졸이 장벽 주변의 유체 흐름 경로에서 벗어나게 되어 에어로졸이 섬유 표면을 때리고 제거될 가능성이 높아집니다.3
이 문서 전체에서 액적 및 입자 크기에 대한 참조는 미크론 단위입니다. 1미크론은 밀리미터의 1/1000 또는 인치의 39/1,000,000입니다.
그림 1은 다양한 재료의 크기를 미크론 단위로 보여줍니다.
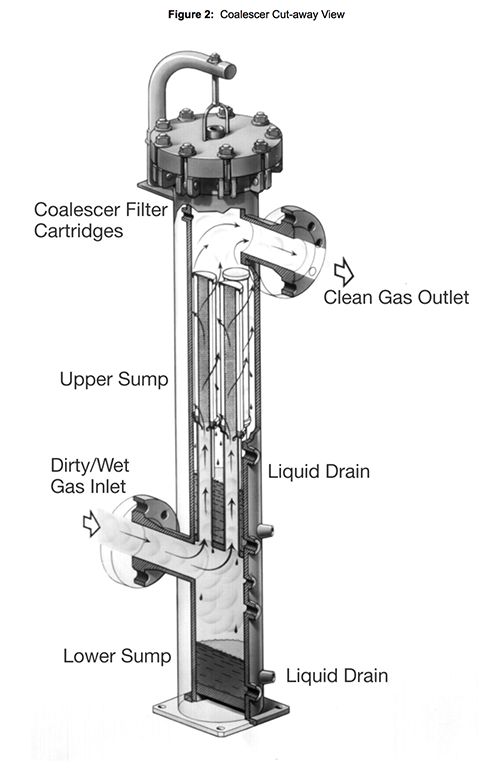
액체/기체 분리 기술
중력 분리기
중력 분리기 또는 녹아웃 드럼에서 중력은 분리를 제어합니다. 기체 속도가 낮고 용기 크기가 클수록 액체/기체 분리가 더 효율적입니다. 침전을 달성하는 데 필요한 큰 용기 크기 때문에 중력 분리기는 300마이크론보다 작은 액적을 제거하도록 거의 설계되지 않습니다⁴. 녹아웃 드럼은 일반적으로 대량 분리 또는 1단계 스크러버로 사용됩니다. 녹아웃 드럼은 릴리프 시스템이나 오염 서비스⁵에서와 같이 용기 내부가 최소한으로 유지되어야 할 때에도 유용합니다. 높은 분리 효율이 필요한 경우 중력 분리기는 제거의 소울 소스로 권장되지 않습니다.
원심분리기
원심 분리기 또는 사이클론 분리기에서 원심력은 중력보다 몇 배 더 큰 힘으로 에어로졸에 작용할 수 있습니다. 일반적으로 사이클론 분리기는 직경이 100μm보다 큰 에어로졸을 제거하는 데 사용되며 적절한 크기의 사이클론은 10μm만큼 낮은 에어로졸의 합리적인 제거 효율을 가질 수 있습니다. 사이클론의 제거 효율은 10μm⁶보다 작은 미스트 입자에서 매우 낮습니다. 사이클론과 녹아웃 드럼은 왁스나 코크스 재료에 권장됩니다.
안개 제거기
미스트 제거기 패드의 고체/액체 가스 분리 메커니즘은 관성 충돌입니다. 일반적으로 섬유 또는 편물 메쉬로 구성된 미스트 제거기 패드는 1-5 미크론까지의 액적을 제거할 수 있지만 이를 포함하는 용기는 액체 재비산을 방지하기 위해 낮은 속도로 작동해야 하기 때문에 상대적으로 큽니다.
필터 베인 분리기
베인 분리기는 단순히 용기 내의 일련의 배플 또는 플레이트입니다. 분리를 다시 제어하는 메커니즘은 관성 충돌입니다. 베인 분리기는 제거 효율을 위해 질량 속도에 민감하지만 일반적으로 미스트 제거기보다 더 높은 속도로 작동할 수 있습니다. 주로 더 효과적인 액체 배수가 액체 재비산을 감소시키기 때문입니다. 그러나 구불구불한 네트워크를 구성하는 플레이트 사이의 상대적으로 큰 경로 때문에 베인 분리기는 상대적으로 큰 액적 크기(10미크론 이상)만 제거할 수 있습니다. 종종 베인 분리기는 가스 속도가 설계 속도를 초과할 때 미스트 제거기 패드 용기를 개조하는 데 사용됩니다.
액체/가스 코어레서
액체/가스 코어레서 카트리지는 미스트 제거기 패드와 베인 분리기의 기능을 결합하지만 일반적으로 대량 액체 제거용으로 지정되지 않습니다. 벌크 액체 시스템에서 고효율 코어레서는 일반적으로 녹아웃 드럼 또는 충돌 분리기의 다운스트림에 배치됩니다. 가스는 액체 배수를 촉진하기 위해 외부 표면에 랩이 있는 결합된 섬유질 재료의 매우 미세한 팩을 통해 흐릅니다(아래 그림 2 참조). 유착기 카트리지는 0.1미크론까지 물방울을 가둘 수 있습니다. 적절하게 설계되고 크기가 조정되면 섬유질 팩에서 응집된 액적을 배출하면 액체 재비산이 없거나 어셈블리 전체에 걸쳐 압력 강하가 증가하지 않는 미스트 제거기 패드 및 베인 분리기의 경우보다 가스 속도가 훨씬 빨라집니다.
표 1은 이러한 각 기술을 요약하고 적절한 선택을 위한 지침을 제공합니다. 보시다시피 5 µm 미만의 매우 미세한 에어로졸이 포함된 시스템의 경우 코어레서를 선택해야 합니다. 가스에서 매우 미세한 에어로졸을 제거하면 압축기 시스템의 주요 경제성, 신뢰성 및 유지보수 이점이 있습니다.
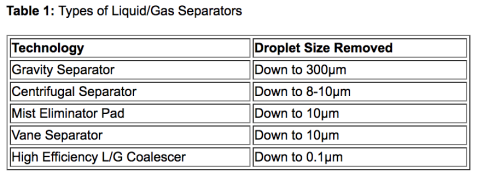
미세 에어로졸의 형성
매우 미세한 액체 에어로졸이 가스 흐름에 들어갈 수 있는 몇 가지 다른 방법이 있습니다.
• 포화 증기로 인한 응축,
• 분무화(흐름 제한을 통한 스프레이 효과) 및,
• 액체 재연행.8
천연 가스 흐름에서 에어로졸 크기 분포에 대한 최근 연구에 따르면 5마이크론 미만의 상당한 양의 액적이 초크 밸브 및 기타 제한 사항이 있을 때마다 또는 증기가 이슬점¹⁰에 있을 때 표준입니다. 그림 3에 표시된 측정은 베인 분리기(중력 분리기와 수평 필터 장벽의 조합 및 미스트 제거기 패드와 등가)의 하류에서 샘플링된 천연 가스 스트림의 액체 에어로졸 농도를 결정하기 위해 수행되었습니다. 결과는 많은 경우에 액적이 너무 작아서 이러한 분리 장치에 의해 가두어지지 않기 때문에 이러한 유형의 분리기를 통과할 수 있음을 보여줍니다. 결과적으로 액체/가스 코어레서는 다운스트림 장비를 보호하거나 귀중한 액체 제품을 회수하기 위해 높은 회수율이 필요할 때마다 선택되는 기술이 되어야 합니다.

등급/사이징
유착기는 미세한 고체 입자의 여과와 가스 스트림에서 액체 에어로졸의 유착을 모두 수행한다는 점에서 필터와 다르다는 점에 유의하는 것이 중요합니다. 액체 제거와 관련된 코어레서의 크기 및 등급 기준은 코어레서의 궁극적인 성능에 매우 중요합니다. 크기가 작은 코어레서는 지속적인 액체 재비산, 매우 낮은 액체 가스 분리 효율을 초래하고 모든 공정 변경에 취약합니다. 코어레서 크기 조정의 중요한 특성은 코어레서에 너무 많은 액체가 가해지면 코어레서 성능이 매우 빠르게 떨어질 수 있음을 보여 주는 그림 4에 설명되어 있습니다(가스 스트림의 높은 에어로졸 농도 또는 높은 가스 유량으로 인해). 이것은 정격 최대값을 초과하면 성능이 점차적으로 감소하는 대부분의 다른 분리 장비에서 극적인 출발을 나타냅니다.
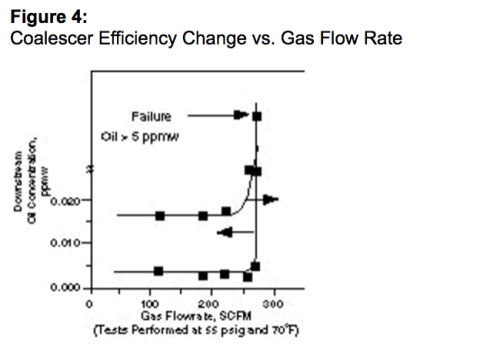
코어레서 성능 검증의 전통적인 수단은 DOP(디옥틸프탈레이트) 테스트¹¹입니다. 이 테스트에서는 제어된 조건에서 DOP 증기의 응축에 의해 직경 0.3 µm의 단분산 에어로졸이 연속적으로 생성됩니다. 에어로졸 생성이 안정화되면(일정한 입자 크기 및 에어로졸 농도) DOP 농도는 광산란 광도계로 유착기의 상류 및 하류에서 측정됩니다. 결과는 사용된 유량에서 DOP 침투의 백분율로 표시됩니다.
DOP 테스트의 몇 가지 주요 단점은 다음과 같습니다.¹²
1. 테스트는 건조 또는 불포화 카트리지에서 수행됩니다. 본질적으로 건식 카트리지는 스펀지와 같은 역할을 하여 카트리지를 통과하는 모든 액체를 흡수합니다. DOP 테스트가 측정하지 않는 것은 액체가 코어레서 매체를 포화시키고 다운스트림으로 다시 비말동반될 수 있을 때 액체를 보유하는 코어레서의 능력입니다.
2. 이것은 두 번째 결점으로 이어집니다. 어셈블리 전체에서 측정된 압력 강하는 포화된 요소 전체의 실제 압력 강하와 비교할 때 과소 평가됩니다. 포화된 DP는 깨끗한 DP보다 약 2-4배 더 큽니다.
3. 테스트는 가스 특성(밀도 및 점도)이 실제 작동 압력에서 지배적인 것과 매우 다른 부분 진공에서 수행됩니다. DOP 테스트 조건은 코어레서 요소의 효율성을 과장하는 경향이 있습니다.
DOP 테스트의 단점을 피하기 위해 Pall은 LASE(Liquid Aerosol Separation Efficiency) 테스트를 개발했습니다. 이 테스트는 정제소 또는 가스 처리 공장에서 볼 수 있는 것과 더 유사한 조건에서 압축 가스 스트림의 코어레서 성능을 측정하기 위한 목적으로만 개발되었습니다. 이 테스트에 사용된 시스템은 그림 5에 개략적으로 나와 있습니다.
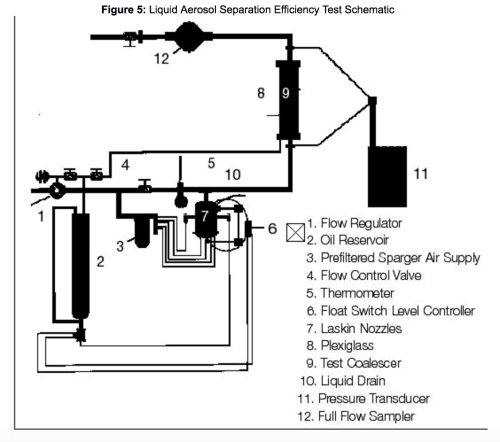
LASE 테스트는 다음과 같은 점에서 DOP 테스트와 다릅니다.
1. 보다 정확하고 의미 있는 효율성 측정을 제공합니다. DOP 효율성은 본질적으로 0.3 µm 디옥틸프탈레이트 액적의 몇 퍼센트가 건식 코어레서에 의해 제거되는지 알려줍니다. LASE 테스트는 코어레서의 가스 다운스트림에 있는 오염 물질의 ppmw를 알려줍니다. 다시 말해, LASE 테스트가 알려주는 것은 다운스트림 장비가 얼마나 많은 오염 물질에 노출될 것인지입니다.
2. DOP는 가스 처리 또는 정제 가스 흐름에서 일반적으로 접하지 않는 액체인 DOP의 단분산(즉, 동일한 크기) 액적을 사용합니다. LASE 테스트는 0.1-0.9 µm 범위의 액적 크기를 가진 윤활유를 사용합니다.
3. LASE 테스트는 포화 카트리지에서 실행되고 양압 하에서 수행되어 공정 조건을 보다 밀접하게 시뮬레이션합니다.
표 2는 DOP와 LASE 테스트의 비교를 보여줍니다.

디자인 및 크기 조정에 미치는 영향
코어레서 설계 개선의 목표는 액체 재비산을 방지하면서 효율성을 극대화하는 것입니다. 재연반은 코어레서 요소에 축적된 액체 방울이 기존 가스에 의해 제거될 때 발생합니다. 이것은 배출 가스의 속도 또는 환상 속도가 배출 액적의 중력을 초과할 때 발생합니다.
이전에 올바른 코어레서 크기 조정의 중요성에 대해 논의했습니다. 코어레서를 설계하고 크기를 조정할 때 다음 매개변수를 고려해야 합니다.
- 매체를 통한 가스 속도,
- 매체를 빠져나가는 가스의 환상 속도,
- 유입 가스의 고체 및 액체 에어로졸 농도,
- 코어레서의 배수성
입구 에어로졸 농도를 제외하고 이러한 각 요소는 제어할 수 있습니다. 일정한 가스 유속에서 매체 속도는 매체 기공 구조의 거칠기를 변경하거나 사용되는 카트리지 수를 늘리거나 줄여서 제어할 수 있습니다. 그러나 매체가 거칠수록 코어레서의 액체 제거 효율이 떨어집니다.
일정한 가스 유량에서 가스의 배출 속도는 용기의 크기 또는 카트리지 사이의 공간을 늘리거나 줄여서 제어할 수 있습니다.
표면 에너지가 낮은 유착기 재료를 선택하거나 유착할 액체의 표면 장력보다 낮은 값으로 매체의 표면 에너지를 낮추는 화학 물질로 유착기 매체를 처리하여 배수를 개선할 수 있습니다¹³. 표면 에너지가 낮은 재료를 사용하면 액체가 필터 매체를 적시는 것을 방지하고 매체의 섬유를 따라 액체의 배수를 가속화합니다. 섬유질 재료에 응집된 액체는 기공에 축적되지 않고 섬유 네트워크를 통해 빠르게 떨어집니다. 그림 6은 화학 처리가 코어레서에 미칠 수 있는 영향을 보여줍니다. 화학 처리된 카트리지의 최대 유속이 처리되지 않은 유사한 카트리지의 2배 이상임을 보여줍니다.

이러한 설계 매개변수로부터 매우 미세한 구멍이 있는 많은 수의 카트리지가 있는 대형 하우징이 가스 흐름에서 발생할 수 있는 액체 문제를 쉽게 제거할 수 있다는 결론을 내릴 수 있습니다. 분명히, 그러한 선박과 관련된 비용은 매우 높습니다. 용기 크기와 카트리지 양이 감소함에 따라 재동반 가능성도 줄어들고 제거 효율성도 떨어집니다. 또한 어셈블리 크기가 감소함에 따라 압력 강하가 증가하여 운영 비용이 증가할 수 있습니다. 따라서 최적화가 필요합니다. 코어레서 어셈블리를 평가할 때 어셈블리의 크기를 결정할 때 이러한 모든 매개변수를 고려해야 합니다. 코어레서는 녹아웃 드럼 또는 기타 충돌 분리기와 함께 사용하는 것이 가장 좋습니다.
액체/가스 코어레서에 대한 현장 테스트
액체를 제거해야 하는 가스 흐름의 현장 테스트는 다음 정보를 제공할 수 있습니다.
1. 기체에 있는 액체의 양,
2. 액체를 효율적으로 합치는 능력, 및
3. 존재하는 고체 입자상 물질의 양.
결과적으로 정확한 샘플링이 중요해집니다. 가스에 존재하는 액체의 양과 특성을 결정하기 위해 테스트 코어레서 카트리지를 통해 가스 유량을 정확하게 측정하는 것이 매우 중요합니다.
이를 위해 완전한 테스트 키트가 사이드 스트림 액체/가스 코어레서 테스트를 수행하도록 설계되었습니다. 이 테스트 키트는 그림 7에 나와 있습니다. 여기에는 다음이 포함됩니다. (1) 작은 볼 밸브로 독립 섬프에 연결된 하나의 카트리지용 코어레서 하우징; (2) 플랜지, 오리피스 플레이트 및 차압 게이지를 포함하는 코어레서 하우징의 다운스트림 오리피스 유량계; (3) 코어레서 하우징을 통한 가스의 흐름을 조절하는 니들 밸브; (4) 유입 및 유출 가스 품질을 분석하기 위해 가스 테스트 키트 중 2개를 동시에 연결할 수 있는 코어레서 하우징의 상류 및 하류에 있는 2개의 샘플 포트; (5) 테스트 키트를 메인 가스 라인과 배출 라인에 연결하는 두 개의 길고 유연한 스테인리스 스틸 호스.

시험 절차
현장 테스트를 위해 현장에 가기 전에 플랜트에 연락하여 시스템 조건(압력, 온도, 가스 유량, 가스 유형 및 가능한 경우 가스 흐름의 액체 농도)을 확인합니다. 이 정보를 기반으로 오리피스 플레이트를 선택하여 표시된 범위의 가스 유량을 측정합니다. 오리피스는 또한 압력 강하를 최소화하도록 선택되어 가스 응축 및 수화물 형성이 유도되지 않습니다.
사이드 스트림 테스트 키트를 온라인으로 배치한 후, 유속은 다시 비말동반되지 않도록 임계 유속 아래로 조정됩니다. 코어레서 카트리지가 포화되면 테스트 지그에 테스트 멤브레인을 코어레서 하우징의 업스트림 및 다운스트림에 삽입하고 섬프에서 카트리지 포화 기간 동안 축적되었을 수 있는 액체를 비우고 실제 테스트를 시작합니다.
테스트가 끝나면 섬프에 축적된 액체의 양이 측정되어 후속 실험실 분석을 위해 샘플 병에 수집됩니다. 테스트 멤브레인은 또한 가스에 부유하는 고형물의 양을 결정하고 고형 오염 물질의 정성적 식별을 위해 수집됩니다. 액체 에어로졸 농도는 응집된 액체의 양과 샘플링된 가스의 양으로 결정됩니다.
필드 테스트 결과
가스 처리 공장과 정제소 모두에서 49개의 가스 스트림(천연 가스, 이산화탄소, 수소 및 연료 가스)에 대한 현장 테스트 결과 대부분의 가스 스트림에 상당한 양의 액체가 존재하는 것으로 나타났습니다. 그림 8은 이러한 테스트 결과를 요약한 것입니다. 테스트한 49개 스트림 중 85% 이상(49개 테스트 중 43개)의 액체 농도가 1ppmw 이상이었습니다. 이러한 농도의 액체는 심각한 회전 장비 문제를 야기할 수 있으며 아민 접촉 장치에서 공정 작동을 불량하게 만들 수 있습니다.

결론
1. 기체/액체 분리 기술을 선택하려면 공정 조건에 대한 지식뿐만 아니라 액체 오염 물질의 특성에 대한 지식이 필요합니다. 액적 크기, 농도, 액체에 왁스가 묻어나거나 오염되는 경향이 있는지 여부를 기준으로 선택해야 합니다.
2. 현장 데이터 분석을 통해 대부분의 가스 공정에서 매우 미세한 액적(1마이크론 미만)이 존재하기 때문에 다운스트림 장비를 보호하기 위해 높은 회수율이 필요할 때마다 고효율 액체/가스 코어레서를 권장해야 하는 것으로 나타났습니다. 귀중한 액체를 회수합니다.
3. 코어레서의 크기와 디자인은 매우 중요합니다. 과도한 에어로졸 농도 또는 큰 가스 유속으로 인해 코어레서에 너무 많은 액체가 사용되면 효율성이 급격히 감소합니다.
4. LASE(Liquid Aerosol Separation Efficiency) 테스트는 실제 작동 조건(포화 요소, 실제 압력 강하 및 가스 특성(밀도, 점도))과 매우 유사한 조건에서 코어레서 카트리지를 테스트할 수 있으므로 액체/기체 코어레서의 의미 있는 성능 테스트입니다. .
5. 유착기 매체의 표면 처리는 섬유질 재료의 액체 배수를 개선하고 주어진 흐름을 처리하는 데 필요한 카트리지 수를 50% 줄였습니다.
6. 현장 테스트에서 상당한 양의 액체가 정제소 및 가스 처리 공장의 가스 흐름에 존재하는 것으로 나타났습니다.
참고문헌
1. CR Pauley, DG Langston 및 FC Betts, "재설계된 필터로 루이지애나 가스 공장에서 거품 발생, 아민 손실 문제 해결," Oil & Gas Journal, 1991년 2월 4일.
2. Perry's Chemical Engineers' Handbook, 6판, McGraw-Hill, New York, 1984, Chap. 18, pp.48-56.
3. Perry's Chemical Engineers' Handbook, 6판, McGraw-Hill, New York, 1984, Chap. 18, pp.48-56.
4. KJ Fewel Jr., JA Kean, "Computer Modeling Aids Separator Retrofit, "Oil & Gas Journal, 1992년 7월 6일.
5. AK Coker, "Computer Program Enhances Guidelines for Gas-Liquid Separation Designs", Oil & Gas Journal, 1993년 5월 10일.
6. Perry's Chemical Engineers' Handbook, 6판, McGraw-Hill, New York, 1984, Chap. 18, pp.48-56.
7. KJ Fewel Jr., JA Kean, "Computer Modeling Aids Separator Retrofit", Oil & Gas Journal, 1992년 7월 6일.
8. Perry's Chemical Engineers' Handbook, 6판, McGraw-Hill, New York, 1984, Chap. 18, pp.48-56.
9. CAG Regan 및 M. Baker, "새로운 분리기/스크러버 설계 프로그램 - 분리 성능에 대한 업스트림 및 다운스트림 장비의 영향", 1992년 5월 14-15일 유럽 챕터, 가스 처리 협회의 제9차 대륙 회의에서 발표된 논문 .
10. Perry's Chemical Engineers' Handbook, 6판, McGraw-Hill, New York, 1984, Chap. 18, pp.48-56.
11. C. Dickenson, "필터 및 여과 핸드북", 3판, Elsevier Adv. Tech, Oxford, 1992, pp. 44-47.
12. K. Williamson, S. Tousi 및 R. Hashemi, "기체/액체 유착기의 성능 평가의 최근 개발", 미국 여과 학회의 제1회 연례 회의에서 발표된 논문, 3월 21-25일, 메릴랜드주 오션 시티.
13. JD Miller, EE Koslow, KW Williamson, 미국 특허 4,676,807, 1987년 6월 30일; id., 미국 특허 4,759,782, 1988년 7월 26일.