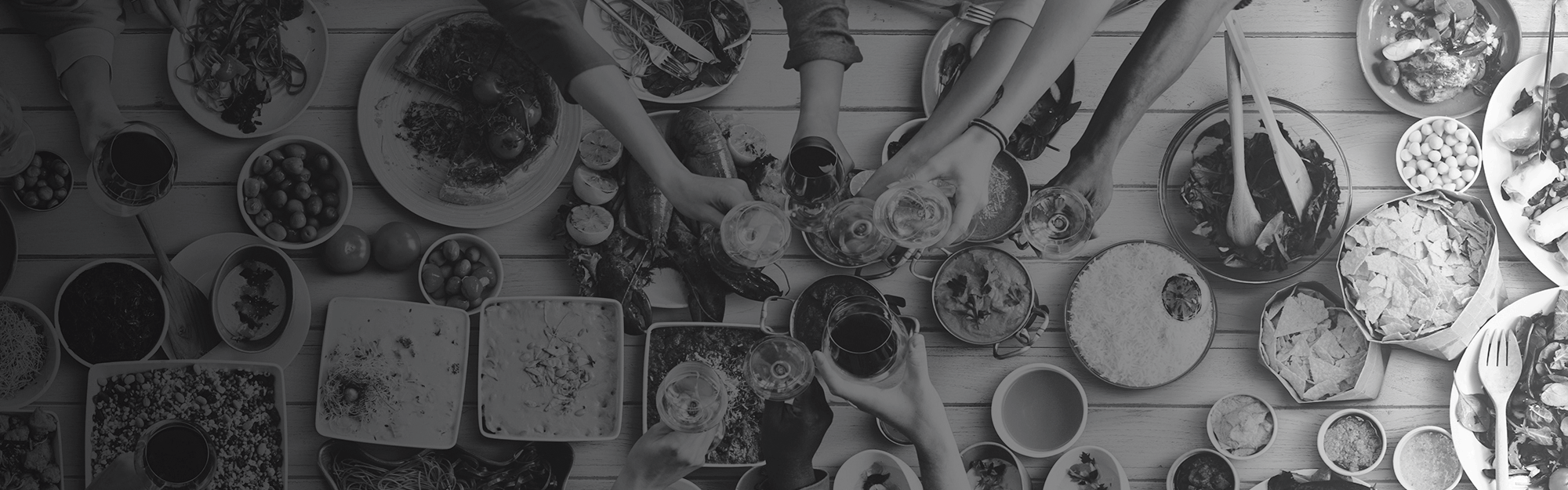
Food For Thought: The Real-Life Success Stories That Improved the Food & Beverage Production Process
August, 2023
From production shifts to unprecedented disruptions to the food and drink supply change to the cost-of-living crisis, it's undeniable that the industry is experiencing some of its most challenging market conditions. Despite this, the global revenue in the food and beverages market grew from $6.7 billion to over $7 billion so far in 2023 according to the report Food and Beverages Global Market Report 2023. Healthy diets and innovative product development are driving this market growth, which makes it imperative for food and beverage producers to examine and improve their processes to remain competitive.
Our goal at Pall Corporation is to help food and beverage manufacturers provide their customers with the best quality products while also reducing costs and supporting green initiatives. We aim to help manufacturers reduce costs, support green initiatives, and ultimately provide their customers with the best quality products.
These real-life success stories have been collected in one place for you to see how our solutions work. On our solutions page, you can discover the following stories:
Australian Winery Recovers High-Value Wine from Lees
Customer Problem: Recovery of wine and juice from lees is a challenging yet unavoidable task for wineries globally. Surging competition and stringent environmental and food safety requirements are intensifying pressure on wineries to filter lees more efficiently and economically.
Pall Solution: By implementing Pall's wine filtration system for lee and juice recovery, this winery recovered more than 1,000 hectolitres of wine.
Brewery Increases Yield and Reduces Waste Streams
Customer Problem: Approximately 80% of the yeast extract collected at the bottom of tanks after fermentation and maturation can be recovered rather than disposed of. The aim of this brewery was to reduce the yeast levels and to recover more beer.
Pall Solution: Installation of a Pall System helped the brewery achieve up to an 80% extract recovery while reducing their environmental impact.
Flavor Manufacturer Reduced Process Time Resulting in 700% Productivity Increase
Customer Problem: A manufacturer of natural flavors filtration process was slow and the quality was inconsistent.
Pall Solution: In this success story, the flavor manufacturer reduces process time by 87% while maintaining filtrate quality by implementing Pall filtration technologies.
A Sixfold Increase in Productivity at a Canadian Whisky Facility
Customer Problem: Due to increased demand for contract bottling projects, this large Canadian distillery faced the need to increase productivity so that additional capacity could be opened up within their plant. This target needed to be accomplished while achieving consistent and excellent filtrate quality and reducing production complexity.
Pall Solution: Using SUPRApak™ technology, this large distillery addresses the challenges caused by sheet filters that negatively affect yield, labor, and productivity.
Dairy Producer Achieves Environmental Impact Reduction Resulting in 40% Reduced Operating Costs
Customer Problem: A dairy producer and processor, located in South America, looked at reducing CIP process costs which totalled more than $400k per year. Additionally, the disposed effluent from CIP still contains a significant amount of caustic (up to 1.0%), while its process required 2.0% caustic.
Pall Solution: By using the Pall Membralox TFF Microfiltration unit, the dairy producer was able to reduce CIP solution discharge by up to 85% therefore reducing operating costs to less than $240k per year.
New Economical Process Delivers Shelf-Stable, High-Quality Cold Brew Coffee For Producer
Customer Problem: Cold brew coffee continues to be one of the beverage industry's fastest-growing markets with a predicted CAGR of 22.7% in the forecast period 2023-2030. With increasing demand, broadening distribution and industry recalls, a cold brew producer needed to implement a new production process to reduce contamination risk while maintaining the flavor characteristics.
Pall Solution: By implementing a 3-stage filtration train from particle removal to sterilizing grade membrane filters, this cold brew coffee producer found an economical and easy-to-use solution to reduce risk of contamination and recall. The solution enabled production of high quality, shelf stable product that maintained flavor characteristics.
We have many more success stories to share! Visit our solutions page for more information on these markets alongside others including non-alcoholic drinks, cider, cannabis oil, dairy, and foods and ingredients.
Subscribe to our blog to stay up-to-date on the latest food and beverage insights and trends
- Category
- Author
- Sort By