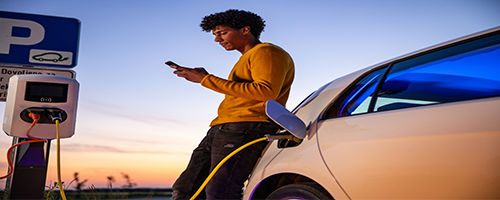
Challenges and Innovations in Manufacturing Lithium Battery Components: Cathode Active Materials for Electric Vehicle Batteries
The cathode active material (CAM) is vital lithium battery component to electric vehicle batteries. It influences the battery's performance, cost, safety, and lifespan. As the demand for electric vehicles continues to rise, the technology trends and challenges of manufacturing cathode active materials are evolving. In this blog post, we will explore the key challenges faced in manufacturing CAM precursors, the final NCM (Nickel, Cobalt, Manganese) CAM, and the innovative solutions being developed to overcome these hurdles.
Segmentation of the Cathode Industry:
The cathode industry is divided into three main categories: performance, standard, and economic.
- Performance CAMs, known as advanced high nickel (NCM), prioritize high energy density.
- Standard CAMs aim to balance between performance and cost, utilizing low-nickel and cobalt-free materials.
- The economic CAMs, such as LFP (Lithium Iron Phosphate) and LFMP (Lithium Iron Manganese Phosphate), focus on affordability and safety.
Evolving Mix of Cathode Chemistries:
The mix of cathode chemistries is shifting in response to market demands. High-nickel NCM cathodes, offering superior energy density, are projected to reach 58% by 2030. LFP cathodes, known for their affordability, are also expected to rise to 42% by 2030, according to findings in the Battery Monitor 2023 Report.
Challenges in Manufacturing CAM Precursors:
- Maintaining Purity: CAM precursors, the building blocks for CAMs, pose several challenges in terms of purity and during the manufacturing processes. The starting materials, typically nickel, manganese, and cobalt, must be of high purity to prevent the formation of electrochemically inert phases (material that does not actively participate in electrochemical reactions) that could hinder the transportation of lithium ions.
- Residence Time: During coprecipitation, filtration solutions must recirculate to build a filter cake. If they don't, they will lose fine particles, affecting the overall process time, particle size, agglomerate formation, homogeneity, and purity of the precipitate, ultimately impacting the precipitate's residence time in the reactor.
- Product Loss: Cleaning the CAM precursor to remove contaminated lye and achieve product purity without product loss is a concern along with water usage, residual moisture, particle form, and energy consumption.
Challenges in Manufacturing Final NCM CAM:
- Precise Chemical Composition: The production of the final NCM CAM involves mixing the CAM precursor with lithium hydroxide or lithium carbonate. Achieving a high reactivity of the battery cell requires almost complete deagglomeration (the breaking down of clusters of particles into finer, individual particles) of the raw materials. Calcination:(thermal treatment under a restricted supply of oxygen) Calcination of the NCM CAM is a further crucial step in the process, which determines the final chemical composition of the NCM.
- Requirement of Pure Gas: The reaction atmosphere and purity of the process gases significantly influence the purity of the final CAM.
- Production of a fine powder: Grinding and classifying larger solid particles during calcination is necessary to produce a fine powder with a consistent size distribution, which is crucial for further processing.
Innovative Solutions and Technologies:
Innovative solutions and technologies are being developed to address these challenges. Special filters are being implemented during CAM production to ensure only high-quality CAMs make it into the final product. Improved filtration systems remove impurities and enhance the purity and consistency of CAMs. Advanced manufacturing processes are being explored to achieve better particle size, crystal structure, uniformity of particle shape, and overall product quality.
Conclusion:
Purity of the cathode active material is critical; the raw material processing or manufacturing process can cause the introduction of impurities in the final cathode material. Manufacturing high-quality CAM precursors and final CAM is crucial for the performance, safety, and longevity of electric vehicle batteries. Overcoming the challenges associated with purity, filtration, and process control is essential for meeting the increasing demands of the electric vehicle market. By developing innovative solutions and technologies, we can ensure the production of powerful and efficient batteries, driving the future of sustainable transportation.
To find out more, visit our dedicated webpage or contact one of our technical experts for advice on the form provided.
Subscribe to our blog to stay up-to-date on the latest insights and trends
- Category
- Author
- Sort By