$60,000 in savings in just eight months
A 775 MW combined-cycle plant in the northeastern United States was experiencing premature plugging of resin pre-coated, backwashable condensate filter cartridges with resin fines and contaminants. The plant needed an experience team to help them eliminate contamination during start-ups. After careful consideration, Pall was chosen for the project. Pall has an international customer base, and a strong reputation for innovative solutions in the power and utilities industry. After attentively surveying the scene, Pall started to put its plan into action.
Hydro-Guard® CoLD R Series Filter Cartridges
Hydro-Guard CoLD R filter elements are manufactured using the CoLD Melt™ fiber production process. The CoLD Melt process permits the creation of multiple filtration zones within a single filter cartridge. The reverse graded pore density, multi-zone design provides customers with even precoating, efficient backflushing, and long filter life. Many power plants around the world have switched from string wound technology to Hydro-Guard CoLD R products for improved condensate polishing.
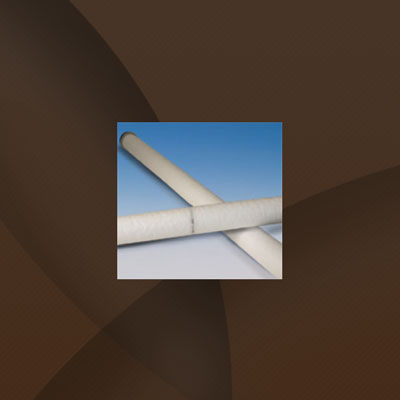
Nuclear Plants
Meeting today’s stringent regulatory requirements and reducing total cost of ownership.
Let’s find the right solution, together.
Let’s connect. We want to share our innovative filtration solutions with you today. Contact our knowledgeable subject matter experts for information on how we can help. Thank you and we look forward to assisting you shortly.